21B Motor (2,8 Ltr.
V6-Einspritz-Motor)
Inhalt
Arbeitspositionen
ALLGEMEINES
Seit Januar 1981 können die
CAPRI-Fahrzeuge auch mit einem 2,8 Ltr. OHV/V6-Motor mit Bosch
K-Jetronic-Einspritzanlage ausgerüstet sein.
OHV = over head valves = obenliegende Ventile
In dieser Gruppe werden nur die Arbeitspositionen des 2,8 Ltr.
Einspritz-Motors beschrieben, die durch den Einbau der Einspritzanlage in
ihrem Reparaturablauf von den bereits in Gruppe 21 des
Capri-Werkstatthandbuches behandelten V6-Motoren abweichen. Außerdem sind
die für diesen Motor erforderlichen Spezialwerkzeuge
und Technischen Daten aufgeführt.
Zur Vereinfachung wird der Motor in den folgenden Beschreibungen, wie
bereits in anderen Werkstatt-Handbüchern, nur kurz mit einem Buchstaben
gekennzeichnet.
Aus untenstehender Tabelle geht hervor, welcher Motor eingebaut ist.
Motoren-Einbauübersicht
Hubraum |
Verdichtung |
Motortyp |
kW
(PS) |
Motorcode
am Motorblock
|
Bezeichnung im
Werkst.-Handbuch
|
2,8
Ltr. |
HC
FI |
OHV/V6 |
118
(160) |
PRN |
C
|
HC = high compression = hohe
Verdichtung = (nur für Super-Kraftstoff geeignet)
Der "C"-Motor ist ein wassergekühlter 6-Zylinder 4-Takt
Ottomotor in 60° V-Form. Die hängenden Ventile werden über Stößel,
Stößelstangen und Kipphebel gesteuert.
Die in Bronzebüchsen gelagerte Nockenwelle liegt zentral im Zylinderblock
und wird über Stirnräder angetrieben.
Das gemeinsame Antriebszahnrad für Zündverteiler und Ölpumpe befindet
sich vor dem hinteren Lager der Nockenwelle.
Die Zylinderköpfe, in denen sich die Verbrennungsräume befinden, haben
Querstromspülung, d. h. frisches Kraftstoff-Luftgemisch wird auf der
einen Seite angesaugt und verbranntes Gas auf der gegenüberliegenden
Seite in den Auspuff geleitet.
Das Axialspiel der vierfach gelagerten Kurbelwelle wird durch
Bundlagerschalen am dritten Lager (Führungslager) bestimmt.
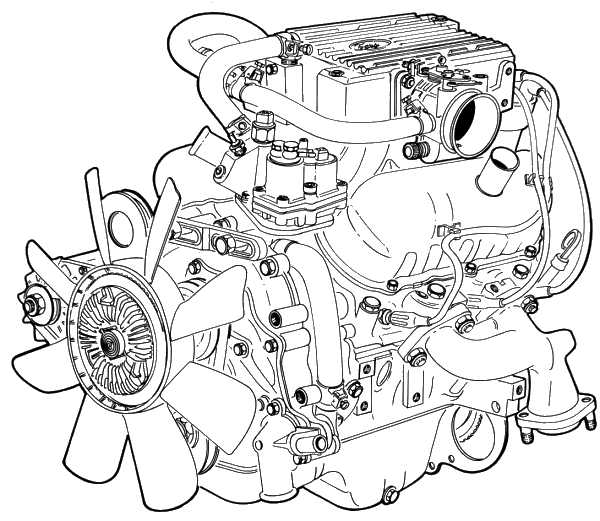
Abb. 1
V6-Einspritz-Motor
Motor-Kennzeichnungscode und
Motorseriennummern
In einigen Ländern ist es gesetzlich vorgeschrieben, dass die
Motoren mit Kennzeichnungscode und Seriennummern versehen sind.
Aus Abb.2 ist zu erkennen, wo die Angaben in den Motor
eingeschlagen sind. Die Buchstaben und Zahlen müssen eine
Mindesthöhe von 6 mm haben. Code und Seriennummer sind so
einzuschlagen (z.B. bei Austauschmotoren), dass sie von einer
prüfenden Dienststelle klar zu erkennen sind.
Die Motornummer besteht
aus einer zweistelligen Vercodung des Baujahres und Monats sowie
einer fünfstelligen Seriennummer (siehe Gruppe 00 TYPENSCHLÜSSEL
im Capri-Werkstatthandbuch). Vor und hinter der kompletten
siebenstelligen Seriennummer ist ein fünfzackiger Stern
eingeschlagen.
Der Motorcode beinhaltet
Hubraum- und Verdichtungsangaben sowie Modellabhängigkeit des
Motors.
Beispiel:
P = 2,8 Ltr.
R = HC-Verdichtung
N = Capri
Das Motorbaudatum ist auf
einer Fläche im Zylinderblock vor dem linken Zylinderkopf
eingeschlagen.
Beispiel:
1B4 = 4. Feb. 1981
|
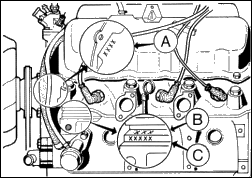
Abb. 2
"C" Motor
A = Baudatum
B = Motorcode
C = Motornummer
|
PRÜFUNG UND EINSTELLUNG
Zum Prüfen des Motorölstandes
muss das Fahrzeug auf einer ebenen Fläche stehen und der Motor
warm sein. Vor der Messung kurze Zeit warten, bis das im Motor
verteilte Öl in die Ölwanne zurückgeflossen ist.
Ölmessstab herausziehen, mit
einem nicht fusselnden Lappen abwischen, dann wieder einsetzen und
nochmals herausziehen (der Ölmessstab muss mit der Öse nach
außen zeigen). Der Ölfilm am Messstab zeigt den jeweiligen
Ölstand in der Ölwanne an, der zwischen den beiden
Markierungsstrichen, Abb.3, liegen muss. Die Nachfüllmenge
zwischen der oberen und unteren Markierung beträgt ca. 0,75 bis
1,0 Ltr..
Falls erforderlich, Motoröl der
vorgeschriebenen FORD-Spezifikation durch die Einfüllöffnung
nachfüllen.
Ein Nachfüllen ist erst dann
erforderlich, wenn der Ölstand die untere Marke erreicht.
Ölstand nicht darunter absinken lassen. Niemals über die obere
Marke Öl nachfüllen, da das zuviel eingefüllte Öl verloren
geht bzw. den Ölverbrauch erhöht.
Motoröl und Hauptstromölfilter
müssen alle 10.000 km erneuert werden. Erschwerte
Einsatzbedingungen, wie Kurzstreckenverkehr, häufiger Kaltstart
und staubige Straßenverhältnisse, bedingen Öl- und
Filterwechsel in kürzeren Abständen.
|
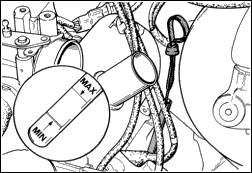
Abb. 3
Ölmessstab
|
Wird nicht das vorgeschriebene
Motoröl verwendet, werden hoher Verschleiß oder Motorschäden
die unausbleiblichen Folgen sein. Der Ölfilm wird unterbrochen
und die stark hitzebeanspruchten Teile verschleißen. In der
Ölwanne sammeln sich Rückstände und verstopfen die Ölkanäle.
Schlechtes Öl hat außerdem keine korrosionshemmende Wirkung, so
dass sich an den Zylinderwänden Rost bildet. Nach nicht allzu
langer Zeit wird der Motor an Leistung verlieren und unnötig
hohen Kraftstoff- und Ölverbrauch aufweisen. Immer nur ein
Markenöl verwenden, dass der FORD-Spezifikation entspricht.
|
SPEZIALWERKZEUGE
21-014
|
Einbauvorrichtung, Kolbenbolzen
|
21-023
|
Universalwelle
(nur in Verbindung mit Montageständer)
|
21-037-A
|
Auszieher, Nadellager Kurbelwelle
|
21-056
|
Ventilfederspanner
|
21-057
|
Ventilhalter
|
21-059
|
Einbaudorn, Kurbelwellendichtring hinten
|
21-063
|
Einbauring, Kurbelwellendichtring vorn
|
21-064
|
Aufspannvorrichtung, Motor
(nur in Verbindung mit 21-023)
|
21-067-A
|
Einpressdorn, Nadellager Kurbelwelle und
Zentrierdorn, Kupplungsreibscheibe
|
21-068
|
Motorhebevorrichtung
|
21-069
|
Einbau- und Zentrierring, Stirnraddeckeldichtring
|
21-070
|
Ausbau- und Zentrierdorn, Stirnraddeckeldichtring
|
21-071 -
21-074
|
Ventilführungsreibahlen, 0,2 - 0,8 mm Übergröße
|
21-092-A
|
Ansaugkopfschlüssel
|
21-096
|
Auszieher, Kurbelwellendichtring vorne
|
ARBEITSPOSITIONEN
|
21 134
MOTOR AUS- UND EINBAUEN |
|
ERFORDERLICHES
SPEZIALWERKZEUG:
Motorhebevorrichtung
............................ |
21-068 |
|
|
Ausbauen
- Massekabel von Batterie und
Motor abklemmen. Motorhaube abbauen (4 Schrauben).
- Kühlmittel ablassen, dazu
unteren Kühlerschlauch vom Wasserpumpenstutzen und oberen
Schlauch vom Wasserauslassstutzen lösen und abziehen, Abb.4.
- Kühlmittelschläuche des
Ausgleichbehälters vom Kühler und vom Zwischenstück des
Zusatzluftschiebers lösen. Ausgleichbehälter vom Halter
abbauen.
- Luftleitblech, Abb.5, und
Luftführung (5 bzw. 4 Schrauben) abschrauben. Kühler abbauen
(4 Schrauben) und mit Luftführung herausheben.
- Heizungsschläuche vom
Zwischenstück des Zusatzluftschiebers und vom
Thermostatgehäuse abbauen, Abb.6.
|
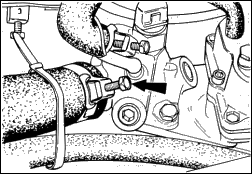
Abb. 4
Oberen Kühlerschlauch lösen
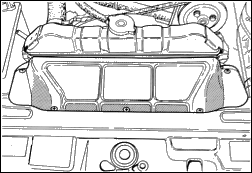
Abb. 5
Luftleitblech ausbauen
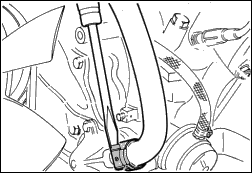
Abb. 6
Heizungsschlauch vom Thermostat-
Gehäuse abbauen
|
- Unterdruckschlauch des
Bremskraftverstärkers vom Luftkammerstutzen abbauen, Abb.7.
- Verbindungsschlauch
Ansauggeräuschdämpfer ausbauen, Gaszug am
Drosselklappenhebel aushängen und mit Halter abbauen (2
Schrauben), Abb.8.
- Kraftstoffleitungen vom
Kraftstoffmengenteiler abschrauben und verschließen, Abb.9.
- Zündkabel von Zündspule
abziehen und Mehrfachstecker am Verteiler trennen.
|
Abb. 7
Unterdruckschlauch Bremskraft-
Verstärker
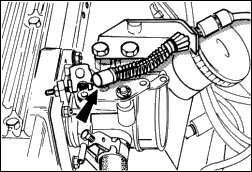
Abb. 8 Gaszug
aushängen
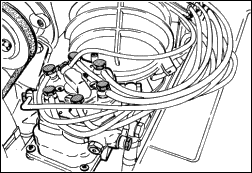
Abb. 9
Kraftstoffleitungen am Mengenteiler
|
- Stromkabel vom Geber
Fernthermometer, Thermozeitschalter, Warmlaufregler,
Zusatzluftschieber und Kaltstartventil abklemmen, Abb.10.
- Öldruckleitung vom
Öldruckanschluss abschrauben.
- Befestigungsschrauben der
Umlenkrolle lösen und Keilriemen abnehmen. Ölpumpe Lenkhilfe
mit Halter vom Motor abbauen (3 Schrauben), Abb.11, zur Seite
legen und mit Draht festbinden.
- Stromkabel von der
Lichtmaschine abklemmen, Lichtmaschine komplett mit Halter
abschrauben und Keilriemen abnehmen.
- Anlasserkabel abklemmen und
Anlasser ausbauen (2 Schrauben), Abb.12.
- Kupplungsseil zurückstellen
und an der Kupplungsschwinge aushängen.
|
Abb.10
Stromkabel abklemmen
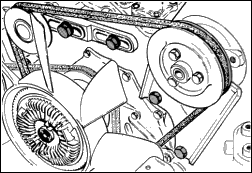
Abb.11 Ölpumpe
Lenkhilfe ausbauen
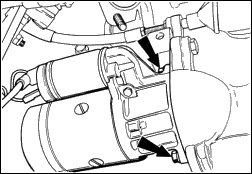
Abb.12 Anlasser
ausbauen
|
- Kühlwasserschläuche vom
Ölkühler abbauen, Abb.13, und Auspuffrohre von den
Auspuffkrümmern abschrauben.
- Beide Gummipuffer der
Motorböcke vom Achskörper abschrauben (2 Muttern), Abb.14.
- Motorhebevorrichtung 21-068 am
Motor anbringen, Abb.15.
- Kupplungsgehäuseabdeckung (1
Schraube mit Mutter) abbauen und Motor vom
Kupplungsgehäuseflansch lösen (6 Schrauben).
- Getriebe abstützen, Motor mit
Motorhebevorrichtung anheben und vorziehen. Rechten
Gummipuffer ausbauen und Motor vorsichtig herausheben.
|
Abb.13
Kühlwasserschläuche am Ölkühler
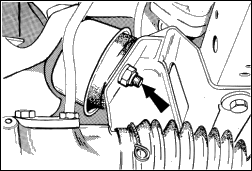
Abb.14
Gummipuffer Motorböcke
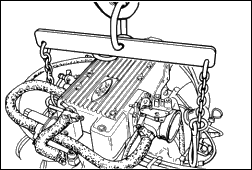
Abb.15
Motorhebevorrichtung 21-068 anbauen
|
Einbauen
- Führungsbuchsen, falls
erforderlich, vom Kupplungsgehäuse an Motorblock umbauen und
Zwischenblech anbringen, Abb.16.
Beachte: Auf richtigen Sitz der Kupplungsschwinge
achten.
- Motor mit Hebevorrichtung
21-068 in das Fahrzeug einsetzen und rechten Gummipuffer am
Motorblock anschrauben. Motor auf die leicht eingefettete
Getriebeantriebswelle aufschieben und mit 2 Schrauben
gleichmäßig am Kupplungsgehäuseflansch beiziehen.
- Alle Flanschschrauben
einsetzen und mit vorgeschriebenem Drehmoment festziehen.
Kupplungsgehäuseabdeckung anbauen.
- Gummipuffer der Motorböcke am
Achskörper anschrauben und Motorhebevorrichtung abbauen.
- Auspuffrohre an die
Auspuffkrümmer anschrauben, Abb.17, und Kühlwasserschläuche
am Ölkühler anbauen.
- Kupplungsseil in
Kupplungsschwinge einhängen und einstellen.
- Anlasser einbauen und
Anlasserkabel anschließen.
- Lichtmaschine mit Halter
einbauen und Stromkabel anschließen.
- Keilriemen auflegen und
spannen, Abb.18.
Beachte: Die Riemenspannung sollte mit einem
Messwerkzeug (falls verfügbar) gemessen werden, siehe Technische
Daten. Andernfalls wird die erforderliche
Keilriemenspannung mit normalem Fingerdruck in der Mitte der
längsten Riemenspannweite gemessen. Gesamtspiel 13 mm.
|
Abb.16
Führungsbuchsen Kupplungsgehäuse

Abb.17
Auspuffrohr anschrauben
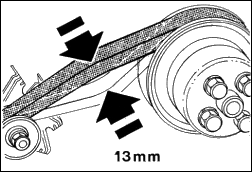
Abb.18
Keilriemen Lichtmaschine spannen
|
- Ölpumpe Lenkhilfe mit Halter
am Motor anbauen. Keilriemen auflegen und spannen (siehe auch Gruppe
13B).
- Öldruckleitung anschließen
und Kraftstoffleitungen am Kraftstoffmengenteiler anschrauben.
- Stromkabel an Geber
Fernthermometer, Thermozeitschalter, Warmlaufregler,
Zusatzluftschieber und Kaltstartventil anschließen.
- Zündkabel auf Zündspule
aufstecken und Mehrfachstecker am Verteiler verbinden.
- Gaszug mit Halter am
Drosselklappenhebel anbauen und Verbindungsschlauch
Ansauggeräuschdämpfer montieren, dabei Einbaulage in Abb.19
beachten.
- Unterdruckschlauch des
Bremskraftverstärkers am Luftkammerstutzen anbringen und
Heizungsschläuche am Zwischenstück des Zusatzluftschiebers
sowie am Thermostatgehäuse befestigen.
- Kühler mit Luftführung
einsetzen, Abb.20, und anbauen. Luftleitblech montieren und
Kühlerschläuche oben und unten befestigen, Abb.21.
- Ausgleichbehälter anbauen und
Kühlmittelschläuche an Kühler und Zwischenstück des
Zusatzluftschiebers anbringen.
- Kühlflüssigkeit und Motoröl
auffüllen.
- Motorhaube anbauen und
einpassen. Massekabel an Motor und Batterie anschließen.
- Motoreinstellung nach
Vorschrift bei Betriebstemperatur vornehmen. Zündzeitpunkt,
Leerlauf und CO-Gehalt einstellen.
|
Abb.19
Verbindungsschlauch Ansauggeräusch-
Dämpfer in Einbaulage
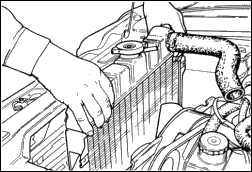
Abb.20 Kühler
einsetzen
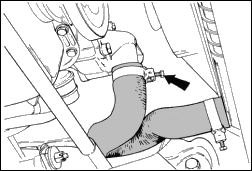
Abb.21
Kühlerschlauch am Wasserpumpen-
Stutzen anbauen
|
Abb.22
"C"-Motor zerlegt
1 = Thermostatgehäuse 6 =
Ansaugkopf
11 = Nadellager Kurbelwelle
2 =
Thermostat
7 = Nockenwellen-Halteplatte 12 =
Radialdichtring
3 =
Wasserpumpe
8 =
Nockenwellenzahnrad
13 = Ölpumpenantriebswelle
4 =
Stirnraddeckel
9 =
Kurbelwellenzahnrad
14 = Führungslager Kurbelwelle
5 =
Bypass-Stutzen
10 =
Starterkranz
15 = Ölpumpe
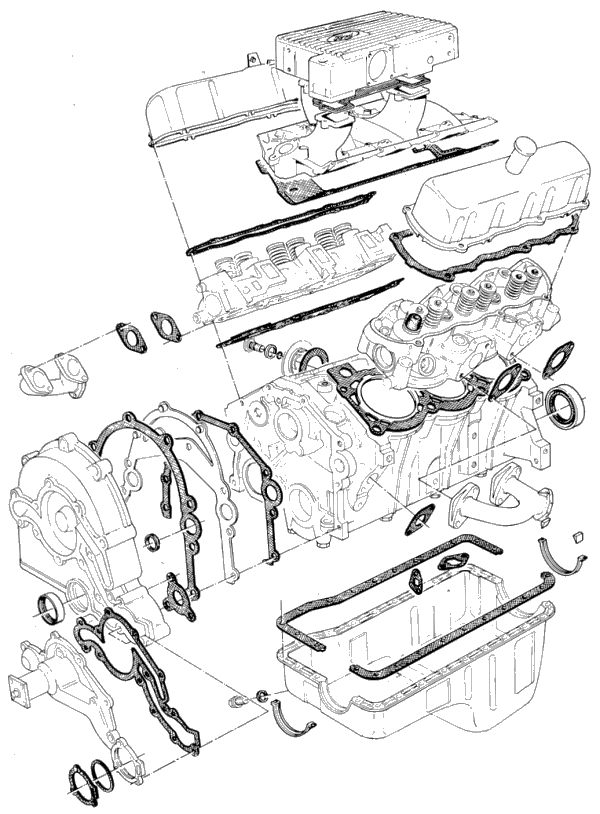
Abb.23
Motordichtungssatz des "C"-Motors
|
|
21 134 8
MOTOR ZERLEGEN UND ZUSAMMENBAUEN |
|
ERFORDERLICHES
SPEZIALWERKZEUG:
Universalwelle
.......................................
Auszieher, Nadellager Kurbelwelle ...........
Einbaudorn, Kurbelwellendichtring ...........
Einbauring, Kurbelwellendichtring vorn ....
Aufspannvorrichtung, Motor ....................
Einpressdorn, Nadellager Kurbelwelle bzw.
Zentrierdorn, Kupplungstreibscheibe .......
Einbau- und Zentrierring, Stirnrad-
deckeldichtring ......................................
Ausbau- und Zentrierdorn, Stirnrad-
deckeldichtring ......................................
Ansaugkopfschlüssel .............................. |
21-023
21-037-A
21-059
21-063
21-064
21-067-A
21-069
21-070
21-092-A |
|
Abb.24 Motor
mit Aufspannvorrichtung 21-064
am Montageständer befestigen
|
Zerlegen
- Linken Auspuffkrümmer
abbauen. Motor mit Aufspannvorrichtung 21-064 und
Universalwelle 21-023 am Montageständer befestigen, Abb.24.
- Motoröl ablassen und
Ölmessstab entfernen. Ölfilter mit handelsüblichem
Spannband abschrauben, Abb.25, und Ölkühler abbauen.
- Kupplungsdruckplatte (6
Schrauben) und Reibscheibe von Schwungscheibe abbauen.
Zwischenplatte Motor hinten abnehmen.
- Zündkerzenstecker abziehen
und Verteilerkappe mit Zündkabel abnehmen. Zündkerzen und
Zündverteiler ausbauen.
- Lüfter (mit 32 mm
Maulschlüssel) und Riemenscheibe (4 Schrauben) von der
Wasserpumpe abbauen, Abb.26.
|
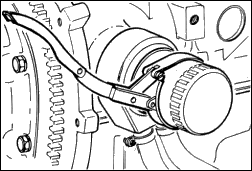
Abb.25
Ölfilter mit Spannband abschrauben
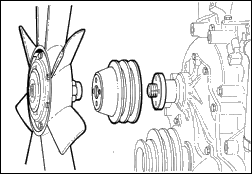
Abb.26 Lüfter
und Riemenscheibe entfernen
|
- Kühlmittelschlauch vom
Zwischenstück des Zusatzluftschiebers und Kraftstoffleitung
vom Kaltstartventil abbauen.
- Motorbelüftungsschlauch von
der Zylinderkopfhaube abziehen und Luftkammer (8 Schrauben)
vom Ansaugkopf abmontieren, Abb.27.
- Bypass-Schlauch am
Thermostatgehäuse entfernen.
- Kraftstoffleitungen von
Einspritzdüsen und Warmlaufregler abschrauben.
Einspritzdüsen ausbauen, Abb.28.
- Spannrolle
Wasserauslassstutzen mit Warmlaufregler abbauen.
- Zylinderkopfhauben (14
Schrauben) mit Kipphebelachsen (6 Schrauben) mit
Ölfangblechen abbauen, Abb.29. Stößelstangen herausnehmen.
Beachte: Stößelstangen und Kipphebelachsen nicht
vertauschen.
- Ansaugkopf (6 Schrauben, 2
Muttern) mit Bypass-Schlauch abschrauben. Falls erforderlich,
Ansaugkopf mit einem Hebel von der Dichtung lösen, Abb.30,
jedoch nicht mit dem Schraubendreher zwischen die
Dichtflächen gehen.
|
Abb.27
Luftkammer abbauen
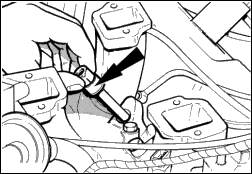
Abb.28
Einspritzdüsen ausbauen
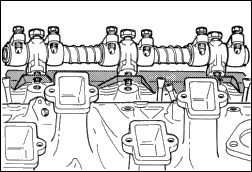
Abb.29
Kipphebelachse mit Ölfangblech
entfernen
|
- Zylinderköpfe abbauen, dabei
Zylinderkopfschrauben in umgekehrter Reihenfolge wie beim
Anziehen lösen (Anzugsreihenfolge siehe Abb.68).
- Öldruckanschluss herausdrehen
und Kurbelwellen-Riemenscheibe (1 Schraube) abbauen.
- Ölwanne nach unten abbauen,
damit kein Ölschlamm und keine Abriebteile in den Motor
gelangen, Abb.31.
- Ölkohlekranz am oberen
Zylinderrand mit einem Schaber entfernen, dabei nicht die
Kolbenringlaufzone berühren.
- Motorblock senkrecht stellen.
Ventilstößel mit einem gebogenen Messingdraht, Abb.32,
herausdrücken, dabei vorher eine größere Ölauffangwanne
unterstellen.
Beachte: Stößel beim Aus- und Einbau nicht
vertauschen.
|
Abb.30
Ansaugkopf mit einem Hebel lösen
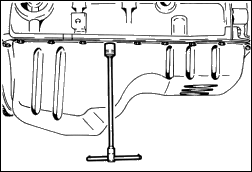
Abb.31 Ölwanne
abschrauben
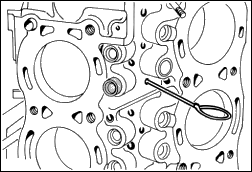
Abb.32
Ventilstößel mit Hilfe eines
Messingdrahtes herausdrücken
|
- Wasserpumpe (13 Schrauben)
abbauen, Abb.33, dabei Thermostatgehäuse (3 Schrauben)
abschrauben und Thermostat herausnehmen. Bypass-Stutzen
abnehmen.
- Stirnraddeckel (9 Schrauben)
abschrauben.
- Nockenwellenzahnrad (1
Schraube) abbauen und Nockenwellenhalteplatte (2 Schrauben)
entfernen. Nockenwelle mit Abstandsring herausziehen.
Scheibenfeder mit Abstandring abbauen.
- Führungshülsen,
Stirnraddeckel Motorblock mit Dichtringen aus dem Motorblock
herausziehen, Abb.34.
- Beide Schrauben der vorderen
Dichtungsplatte entfernen, Abb.35. Zwischenplatte abnehmen.
- Motor weiter schwenken, um
Restbestände an Öl, der entfernten Ölkohle und
Kühlflüssigkeit aufzufangen.
|
Abb.33
Wasserpumpe abbauen
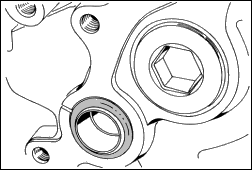
Abb.34
Führungshülse am Motorblock
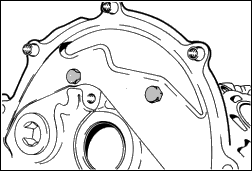
Abb.35
Zwischenplatte abschrauben
|
- Ölpumpe mit Ansaugrohr (2
Schrauben) abbauen, Abb.36, und Antriebswelle herausziehen.
- Kurbelwellenzahnrad mit
handelsüblichem Werkzeug abziehen, Abb.37.
- Kennzeichnung aller Pleuel-
und Hauptlagerdeckel für den späteren Wiedereinbau
überprüfen, Abb.38.
- Pleuellagerdeckel einzeln mit
Lagerschalen abbauen. Kolben mit Pleuelstangen und
Lagerschalen zusammen aus dem Motor drücken. Sollten die
Lagerschalen der Pleuelstangen vor Ausbau der Kolben entnommen
werden, sind diese entsprechend der Pleuelstangen, zwecks
eventuellem Wiedereinbau, zu kennzeichnen.
|
Abb.36 Ölpumpe
mit Saugrohr abbauen
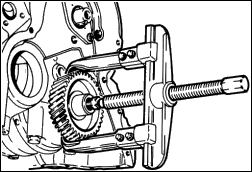
Abb.37
Kurbelwellenzahnrad abziehen
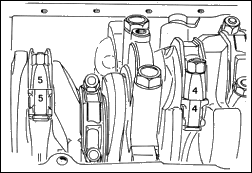
Abb.38
Kennzeichnung der Pleuellager
|
- Nadellager Kurbelwelle mit
Spezialwerkzeug 21-037-A aus der Kurbelwelle ziehen, Abb.39.
- Schwungscheibe (6 Schrauben)
abschrauben.
- Hauptlagerdeckel mit
zugehörigen Lagerschalen abbauen. Beim Abbau des
Führungslagerdeckels auf den Sitz der Bundlagerschalen achten
und dementsprechend kennzeichnen.
- Kurbelwelle aus dem
Zylinderblock heben und hinteren Radialdichtring abnehmen,
Abb.40.
- Lagerschalen aus dem
Zylinderblock nehmen und zwecks eventueller Wiederverwendung
kennzeichnen.
- Radialdichtring des
Stirnraddeckels mit Spezialwerkzeug 21-069 und 21-070
auswechseln, Abb.41.
|
Abb.39
Nadellager Kurbelwelle mit Spezial-
Werkzeug 21-037-A ausbauen
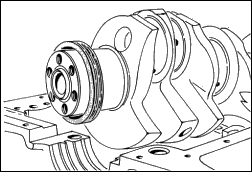
Abb.40
Kurbelwelle mit Radialdichtring aus
dem Zylinderblock heben
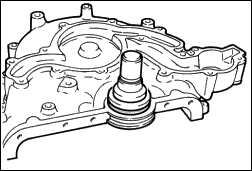
Abb.41
Radialdichtring auswechseln
|
Zusammenbauen
Laufzeit, eventueller
Motorschadensumfang sowie die beabsichtigte weitere Verwendung von
Einzelteilen bestimmen Grad und Art der Reinigung, die dem
Zusammenbau vorausgehen muss. Hierbei ist besonders der
Zylinderblock mit seinen Ecken, Winkeln und Bohrungen betroffen.
Alle Verschlussstopfen und Deckel gegebenenfalls entfernen und
deren Sitze mit geeigneten Reinigungsmitteln und Werkzeugen
(Bürsten, Schaber) reinigen. Besonders die Ölkanäle, z.B. von
Zylinderblock, Zylinderkopf usw. müssen frei von Schmutz und
Spänen sein, Abb.42. Falls eingepresste Verschlussdeckel und
Wasserstopfen entfernt wurden, so sind diese, wie auch alle
anderen Dichtungen, grundsätzlich bei jeder Motorreparatur durch
Neue zu ersetzen.
Kurbelwelle lagern
Grundbohrung im Zylinderblock
Die Grundbohrung im Zylinderblock
hat bei Standardmaß keine Kennzeichnung. Bei Bohrungen mit 0,38
mm Übergröße sind die Lagerdeckel mit einem weißen Farbstrich,
Abb.43, gekennzeichnet.
Hauptlagerzapfen der
Kurbelwelle
Die Hauptlagerzapfen der
Kurbelwelle haben bei Standard-Durchmesser keine Kennzeichnung.
Bei Lagerzapfen mit 0,25 mm Untermaß ist die Kurbelwelle am 1.
Gegengewicht mit einem grünen Farbstrich gekennzeichnet.
Achtung: Beim Capri 2,8 Injection dürfen nur Kurbelwellen
mit an Haupt- und Pleuellagerzapfen festgewalzten Übergangsradien
verbaut werden.
Diese festgewalzten Kurbelwellen dürfen an den Haupt- und
Pleuellagerzapfen nur bis max. 0,254 mm Untermaß geschliffen
werden.
|
Abb.42
Ölkreislauf
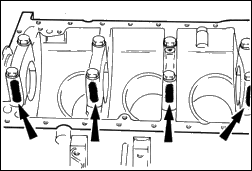
Abb.43
Farbmarkierung Hauptlagerdeckel
|
Pleuellagerzapfen der Kurbelwelle
Die Pleuellagerzapfen der
Kurbelwelle haben bei Standard-Durchmesser ebenfalls keine
Kennzeichnung. Bei Pleuelzapfen mit 0,25 mm Untermaß ist die
Kurbelwelle an der 1. Wange zum Pleuelzapfen mit einem grünen
Farbpunkt gekennzeichnet, Abb.44.
Kurbelwellen, deren Haupt- und Pleuellagerzapfen auf
Untermaß geschliffen sind, haben sowohl den Farbstrich als auch
den Farbpunkt vorn an der Breitseite der 1. Wange, Abb.45.
Lagerschalen
Standard Haupt- und
Pleuellagerschalen erhalten keine Farbkennzeichnung. Lagerschalen
für Untermaß-Kurbelwellen bzw. Übergröße-Zylinderköpfe sind
auf der Rückseite entsprechend beschriftet (siehe
Ersatzteil-Microfilm) und im Falle von
Produktions-Reparatur-Größen seitlich an der Außenkante
farblich gekennzeichnet, Abb.46. Die reinen Service-Haupt- und
Pleuellagerschalen (0,5, 0,75 und 1,0 mm
Untermaß-Kurbelwellenzapfen) dürfen nicht verbaut werden.
Bei der Auswahl von neuen Lagerschalen muss in jedem Fall die
Zugehörigkeit im Ersatzteil-Mikrofilm überprüft und ausgemessen
werden!
Um in den Grenzen des vorgeschriebenen Lagerspieles (siehe
Technische Daten) zu bleiben, müssen Lagerzapfen und Bohrungen
mit Lagerschalen einzeln vermessen werden.
|
Abb.44
Farbmarkierung Pleuellagerzapfen
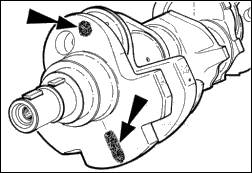
Abb.45
Farbmarkierungen Haupt- und
Pleuellagerzapfen
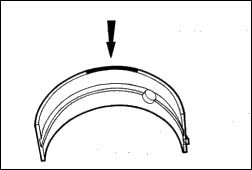
Abb.46
Farbmarkierungen Lagerschale
(Produktions-Reparaturgröße)
|
Ermitteln des Lagerspieles
Das Ausmessen der Lager (auch bei
Untermaß-Kurbelwellen) kann entfallen und die Bestimmung der
erforderlichen Lagerschalen wird wesentlich erleichtert, wenn
"PLASTIGAGE" (Type PG-1) der Firma:
PERFECT CIRCLE CORPORATION
HAGERSTOWN, INDIANA/USA
verwendet wird.
"PLASTIGAGE" ist die Bezeichnung für einen genau
kalibrierten Kunststofffaden.
Auslieferer: Bundesrepublik Deutschland
Fa. K. H. Ern/Motorenteile GmbH
Schinkelstr. 46 - 48
D-4000 Düsseldorf
Tel. 0211/353536
Auslieferer: Großbritannien
Norman Gaydon
68 London Road
Southend-on-Sea
Essex SS1 1PG
Voraussetzungen
für eine Messung mit "PLASTIGAGE": a)
Die Lagerstelle muss öltrocken und sauber
sein.
b) Die Kurbelwelle darf während des
Messvorganges nicht gedreht werde.
c) Die Messstelle soll dicht neben der
jeweiligen Totpunktstellung liegen.
d) Auf die Lagerdeckel darf nicht geschlagen
werden. Ein
Stück dieses Fadens in Lagerbreite auf den
Kurbelwellen-Hauptlager- oder Pleuellagerzapfen legen, Abb.47,
dann Haupt- oder Pleuellagerdeckel mit Lagerschale aufsetzen und
mit dem vorgeschriebenen Drehmoment festziehen. Je nach Lagerspiel
wird der Kunststofffaden mehr oder weniger gepresst. Lagerdeckel
wieder entfernen.
Jede Lagerstelle der Hauptlager muss einzeln vermessen werden,
wobei die restlichen Lagerdeckel nicht montiert sein dürfen.
Die Breite des gequetschten Kunststofffadens ist mit einer auf der
PLASTIGAGE-Packung aufgedruckten Skala, Abb.47, messbar; der
Messwert entspricht dem Lagerspiel.
Grundsätzlich nur einwandfreie Schrauben zur Lagerung der
Kurbelwelle verwenden. Diese nicht höher als mit dem
vorgeschriebenen Drehmoment festziehen!
|
Ermitteln des Kolbenspieles
a) Hauptlagerdeckel ohne
Lagerschalen
aufsetzen und mit vorgeschriebenem
Drehmoment festdrehen.
b) Den eingelaufenen Motorblock um 180°
schwenken und Zylinderbahnen mit
handelsüblichem Messwerkzeug aus-
messen.
c) Ist der ermittelte Durchmesser der
Zylinderbahn gegenüber der Kolben-
klassifizierung des gelaufenen Kolbens
zu groß, so muss der Motorblock
überholt oder ausgetauscht werden.
Motorblock mit neuen Kolben ent-
sprechender Zylinderbahnklassifizierung
bestücken.
d) Vor Einbau der Kolben das Stoßspiel der
Kolbenringe überprüfen, Abb.48. Die
angegebenen Maße, siehe Technische
Daten, beziehen
sich auf den in der
Produktion verwendeten Lehrenring und
können im Zylinder gemessen um 0,15 mm
überschritten werden.
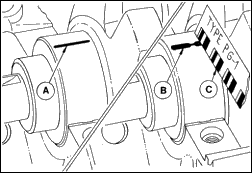
Abb.47 Ausmessen
des Lagerspiels
A = kalibrierter Kunststofffaden
B = gequetschter Kunststofffaden
C = Messskala
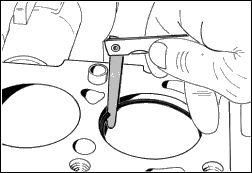
Abb.48 Stoßspiel
der Kolbenringe prüfen
|
- Neues Nadellager mit
Spezialwerkzeug 21-067-A in die Kurbelwelle einpressen, Abb.49.
Kurbelwellenzahnrad aufsetzen und mit der Riemenscheibe
aufziehen.
- Zylinderblock-Hauptlagerschalen
trocken in den Block einsetzen, dann mit Motoröl benetzen und
Kurbelwelle einlegen.
- Hauptlagerdeckel komplett mit
eingeölten Lagerschalen aufsetzen. Am Führungslager
Bundlagerschalen eingelegt, Abb.50. Hinteren Hauptlagerdeckel am
hinteren Teil der Auflagefläche, Abb.51, vorher dünn mit
Dichtungsmasse (Teil-Nr. A 70SX-19554-BA) bestreichen.
Beachte: Der Pfeil auf den Hauptlagerdeckeln muss zur
Stirndeckelseite des Motors zeigen.
- Schrauben der Lagerdeckel
gleichmäßig mit vorgeschriebenem Drehmoment festdrehen. Am
Führungslagerdeckel Schrauben nur fingerfest beidrehen.
Kurbelwelle erst bis zum Anschlag nach hinten drücken, dann
langsam bis zum Anschlag nach vorne drücken und festhalten. In
dieser Stellung Schrauben des Führungslagerdeckels mit
Drehmoment festziehen (dieser Arbeitsvorgang ist erforderlich,
um die Bundlagerschalen zum gleichmäßigen Tragen zu bringen).
|
Abb.49 Nadellager
Kurbelwelle mit
Spezialwerkzeug 21-067-A einpressen
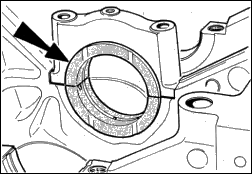
Abb.50
Bundlagerschalen am Führungslager
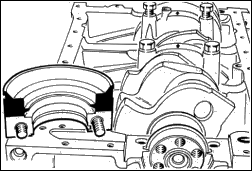
Abb.51 Hinteren
Hauptlagerdeckel mit
Dichtungsmasse bestreichen
|
- Axialspiel der Kurbelwelle,
siehe Technische Daten, mit
einer handelsüblichen Messuhr prüfen, Abb.52, und ggf.
Bundlagerschalen austauschen.
- Neuen hinteren Radialdichtring
an der Dichtlippe mit Motoröl benetzen, auf das Spezialwerkzeug
21-059 schieben und bis zum Anschlag des hinteren
Kurbelwellenlagers treiben, Abb.53.
- Dichtkeile des hinteren
Hauptlagerdeckels mit Dichtungsmasse (Teil-Nr. A 70SX-19554-BA)
bestreichen und mit einem stumpfen Schraubendreher eintreiben,
Abb.54 (die runde Seite des Dichtkeiles ist mit einer roten
Farbkennzeichnung versehen und muss bei der Montage zum
Lagerdeckel zeigen).
- Motor drehen und
Nockenwellenlager, Nockenwelle und Halteplatte mit Öl benetzen.
|
Abb.52 Axialspiel
der Kurbelwelle ermitteln
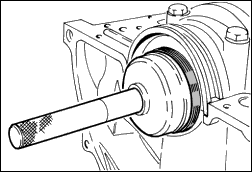
Abb.53
Radialdichtring mit Spezialwerkzeug
21-059 einpressen
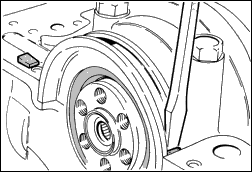
Abb.54 Dichtkeile
des hinteren Hauptlager-
Deckels montieren
|
- Nockenwelle vorsichtig vom
vorderen Lager her einbauen, Abb.55. Vor dem Einbau den
Abstandring mit der Fasenseite auf die Nockenwelle schieben und
Scheibenfeder einsetzen. Halteplatte mit selbstsichernden
Schrauben und vorgeschriebenem Drehmoment festdrehen.
- Zylinderblockstirnseite am
äußeren Umfang sowie die Rückseite der vorderen
Zwischenplatte mit Dichtungsmasse bestreichen. Dichtung auflegen
und Zwischenplatte zunächst nur handfest an den Zylinderblock
montieren, Abb.56. Zur Führung zwei weitere Schrauben in die
unteren Bohrungen der Zwischenplatte schrauben und nach dem
Festziehen der Zwischenplatte wieder entfernen.
- Beide Führungshülsen mit
aufgeschobenen Dichtringen ohne Dichtungsmasse in den
Zylinderblock einführen, wobei die angefaste Seite der
Führungshülse zum Stirnraddeckel zeigen muss, Abb.57.
|
Abb.55
Nockenwelle einbauen
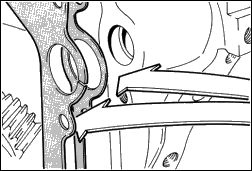
Abb.56
Zwischenplatte mit Dichtung
montieren
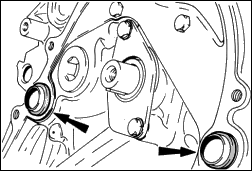
Abb.57
Führungshülsen mit Dichtringen
montiert
|
- Nockenwellenzahnrad mit der
Punktmarke deckend zur Marke auf dem Kurbelwellenzahnrad
aufschieben (Scheibenfedernuten müssen gegeneinander stehen),
dabei die Kurbelwelle etwas hin- und herdrehen, damit sich das
Nockenwellenzahnrad leichter aufschieben lässt. Schraube mit
Scheibe eindrehen und mit vorgeschriebenem Drehmoment
festziehen.
Beachte: Da das Kurbelwellenzahnrad zwei Markierungen
hat, Nockenwellenzahnrad nur so montieren, wie in Abb.58 gezeigt
wird.
- Axialspiel der Nockenwelle mit
einer handelsüblichen Tastuhr prüfen, Abb.59, dann an vier
Stellen des Zahnrades das Zahnflankenspiel messen, siehe Technische
Daten.
- Stirnraddeckeldichtfläche am
äußeren Umfang sowie Vorderseite der Zwischenplatte mit
Dichtungsmasse bestreichen.
- Dichtung auflegen und
Stirnraddeckel aufsetzen, dabei Deckel mit Hilfe des
Spezialwerkzeuges 21-069 und der Kurbelwellen-Riemenscheibe
zentrieren, Abb.60. Schrauben mit vorgeschriebenem Drehmoment
festdrehen.
- Kurbelwellen-Riemenscheibe
montieren und mit vorgeschriebenem Drehmoment festdrehen.
Beachte: Unterlegscheibe Riemenscheibe einseitig mit
Dichtungsmasse bestreichen.
- Wasserpumpe mit Dichtung anbauen
und Thermostat einsetzen. Thermostatgehäuse und Bypass-Stutzen
mit Dichtung montieren.
|
Abb.58
Punktmarkierung Nocken- und
Kurbelwellenzahnrad
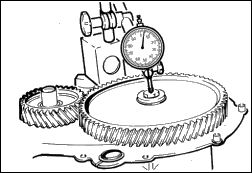
Abb.59 Axialspiel
der Nockenwelle prüfen
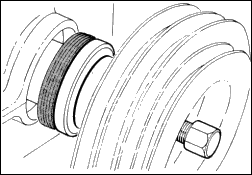
Abb.60
Stirnraddeckel mit Spezialwerkzeug
21-069 und Kurbelwellen-
Riemenscheibe zentrieren
|
- Motor schwenken, Zwischenplatte
ansetzen und Schwungscheibe mit vorgeschriebenem Drehmoment
anbauen, Abb.61.
Beachte: Nur einwandfreie und eingeölte Schrauben
wiederverwenden.
- Kolben und Zylinderbahnen mit
Motoröl benetzen. Kolbenringstöße mit vorgeschriebenen
Abstand, siehe Technische Daten,
zueinander verdrehen.
- Kolbenringe mit handelsüblichem
Werkzeug (Spannband) zusammenziehen. Kolben mit einem
Hammerstiel in den Zylinder drücken, Abb.62, dabei die Pleuel
mit der Hand auf die Pleuelzapfen führen.
Beachte: Bei der Montage muss die Frontmarkierung der
Kolben (Pfeil, Kerbe usw.) in Fahrtrichtung zeigen.
- Motor schwenken.
Pleuelstangen-Lagerschalen einlegen, einölen und fest gegen die
Pleuelzapfen drücken.
- Pleuel-Lagerdeckel mit
eingeölten Lagerschalen aufstecken. Pleuelmuttern mit
vorgeschriebenem Drehmoment festdrehen, Abb.63.
Beachte: Überprüfen, ob die Pleuel auf dem Pleuelzapfen
genügend axiales Spiel haben.
|
Abb.61
Schwungscheibe befestigen
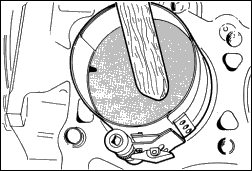
Abb.62 Kolben mit
Spannband einbauen

Abb.63
Pleuelmuttern mit vorgeschriebenem
Drehmoment festdrehen
|
- Antriebswelle Ölpumpe mit
aufgepresster Haltescheibe (Richtung und Abstand beachten), mit
der spitzen Seite zum Verteiler zeigend, in den Zylinderblock
einführen, Abb.64.
- Ölpumpe komplett mit Ansaugrohr
aufsetzen und Schrauben mit vorgeschriebenem Drehmoment
festdrehen, Abb.65.
Beachte: Bei Verwendung einer überholten Ölpumpe ist
diese vor dem Einbau von Hand durchzudrehen und mit Motoröl zu
füllen.
- Gummidichtung in die Nut des
hinteren Hauptlagerdeckels und in den Stirnraddeckel einsetzen.
Zylinderblockdichtfläche am Stoß des Stirnraddeckels mit
Dichtmasse bestreichen. Ölwannendichtung auflegen und die Nasen
der Korkdichtung unter die Aussparung in der Gummidichtung
schieben, Abb.66.
|
Abb.64
Antriebswelle Ölpumpe
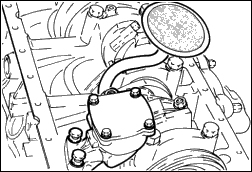
Abb.65 Ölpumpe
montieren
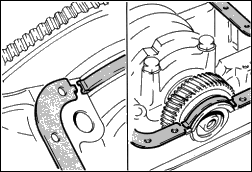
Abb.66
Ölwannendichtung
|
- Ölwanne aufsetzen. Schrauben
eindrehen und mit vorgeschriebenem Drehmoment in zwei Stufen
anziehen, siehe Technische Daten.
- Ölablassschraube mit neuer
Dichtung und vorgeschriebenem Drehmoment festziehen.
Beachte: Bei jedem Ölwechsel und Lösen der
Ölablassschraube ist ein neuer Dichtring zu verwenden.
- Motor schwenken, Ventilstößel
mit Öl benetzen und in den Zylinderblock einsetzen.
- Zylinderkopfdichtungen über die
Führungshülsen auf den Zylinderblock legen, Abb.67. Linke und
rechte Zylinderblockdichtung sind unterschiedlich.
Beachte: Die Dichtungen sind mit "OBEN VORN"
gekennzeichnet.
Ersatzteil-Nr. beachten!
- Komplette Zylinderköpfe auf
aufsetzen. Schrauben (an Kopf und Gewinde eingeölt) einführen
und nach Schema, Abb.68, mit vorgeschriebenem Drehmoment in drei
Stufen festziehen, siehe Technische
Daten.
- Die vier Stoßstellen von
Zylinderblock, Zylinderköpfen und Ansaugkopf mit Dichtmasse
bestreichen, Abb.69, und neue Ansaugkopfdichtung auflegen.
|
Abb.67
Zylinderkopfdichtungen auflegen
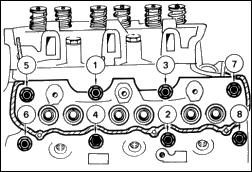
Abb.68
Anzugsreihenfolge Zylinderkopf
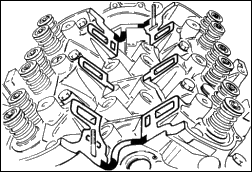
Abb.69
Stoßflächen mit Dichtungsmasse
bestreichen
|
- Ansaugkopf aufsetzen, Schrauben
einführen und mit vorgeschriebenem Drehmoment, siehe Technische
Daten, in vier Stufen nach Schema in Abb.70 festdrehen.
- Stößelstangen an beiden Enden
mit Motoröl benetzen und in die Ventilstößelpfannen stellen.
Ölfangbleche und Kipphebelachsen aufsetzen, Abb.71, dabei
Stellschrauben der Kipphebel in die Stößelstangenpfannen
führen. Schrauben der Kipphebelachsen beidrehen und mit
vorgeschriebenem Drehmoment anziehen.
- Bypass-Schlauch am
Thermostatgehäuse befestigen.
- Motor auf O.T. des 1. Zylinders
stellen und Zündverteiler einbauen.
- Ventilspiel einstellen, siehe Arbeitsposition
21 213.
- Zylinderkopfhauben
vorschriftsmäßig montieren. Spannrolle sowie
Wasserauslassstutzen mit neuer Dichtung anbauen.
- Einspritzdüsen einbauen und
Kraftstoffleitungen an Düsen und Warmlaufregler anschrauben.
- Ölkühler wie folgt einbauen:
a) Neue Gewindebuchse, "A" in Abb.72,
in den Zylinderblock einschrauben.
b) Omnifit-Aktivator "Rapid" gemäß Ford-
Spezifikation SSM-99B-9000-AA auf
die Gewindegänge der Buchse, "A"
in
Abb.72, sowie in die neue Gewinde-
hülse, "D" in Abb.72, auftragen.
c) Omnifit-Dichtmittel "300 Rapid" gemäß
Ford-Spezifikation SSM-4G-9003-AA
nur auf die vorderen Gewindegänge
der aus dem Zylinderblock ragenden
Gewindebuchse auftragen.
Beachte: Nur 1 Tropfen Dichtmittel auftragen, um zu
verhindern, dass Dichtmittel in den Ölkreislauf gelangt.
|
Abb.70
Anzugsreihenfolge Ansaugkopf
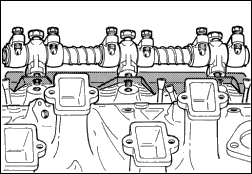
Abb.71
Kipphebelachse mit Ölfangblech
anbauen
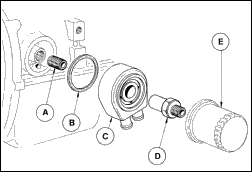
Abb.72
Einzelteile Ölkühler und
Hauptstromölfilter
A = Gewindebuchse
B = Dichtung
C = Ölkühler
D = Gewindehülse
E = Hauptstromölfilter
|
d) Neuen Dichtring "B"
in Abb.72
und Ölkühler "C" in Abb.72 an-
setzen und mit Gewindehülse
"D" in Abb.72 befestigen. Beim
Festziehen der Hülse mit vorge-
schriebenem Drehmoment auf
die Stellung des Ölkühlers zur
hinteren, senkrechten Kante des
Zylinderblocks achten, Abb.73.
- Neue Ölfilterpatrone
aufschrauben, bis die Gummidichtung mit dem Gehäuse Kontakt
hat, dann noch 3/4 Umdrehung festziehen. Gummidichtung vor der
Montage mit Motoröl benetzen.
- Öldruckanschluss eindrehen und
mit vorgeschriebenem Drehmoment festziehen.
- Luftkammer mit neuer Dichtung an
den Ansaugkopf montieren und Motorbelüftungsschlauch an
Zylinderkopfhaube anbringen.
- Kraftstoffleitung an
Kaltstartventil und Kühlmittelschlauch am Zwischenstück des
Zusatzluftschiebers anbauen.
- Lüfter und Riemenscheibe an der
Wasserpumpe anbauen.
- Zündkerzen einschrauben und mit
vorgeschriebenem Drehmoment festziehen. Verteilerkappe aufsetzen
und Zündkabel in gezeigter Anordnung, Abb.74, auf die
Zündkerzen stecken.
- Reibscheibe mit Spezialwerkzeug
21-067-A zentrieren, Abb.75. Druckplatte auf die Passstifte
aufsetzen und mit vorgeschriebenem Drehmoment festziehen.
- Ölmessstab einschieben und
Motor vom Montageständer abbauen.
- Linken Auspuffkrümmer mit neuen
Dichtungen anbauen.
|
Abb.73 Einbaulage
des Ölkühlers
A = Hintere Kante des Zylinderblocks
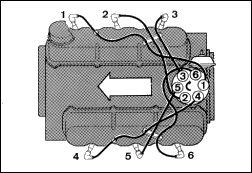
Abb.74
Zündkabelanordnung (Zündfolge)
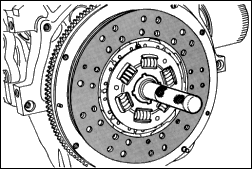
Abb.75
Reibscheibe mit Spezialwerkzeug
21-067-A zentrieren
|
|
21 154
ÖLWANNE AB- UND ANBAUEN |
|
KEIN
SPEZIALWERKZEUG ERFORDERLICH
|
|
Abbauen
- Massekabel von der Batterie
abklemmen. Verteilerkappe abnehmen und Luftführung vom
Kühler abschrauben.
- Motoröl ablassen.
Anlasserkabel abklemmen und Anlasser ausbauen (2 Schrauben).
- Beide Gummipuffer der
Motorblöcke vom Achskörper abschrauben (2 Muttern), Abb.76,
und Kupplungsgehäuseabdeckung entfernen.
- Ölwannenschrauben (24)
herausdrehen und Ölwanne vom Motorblock lösen. Festsitzende
Ölwanne seitlich mit einem Schraubendreher abdrücken.
- Motor anheben und am Getriebe
abstützen, Ölwanne herausnehmen.
Beachte: Motor nur so weit anheben, dass die Ölwanne
herausgenommen werden kann.
Anbauen
- Dichtflächen des Motorblocks
und der Ölwanne von alten Dichtungsresten reinigen. Eventuell
verbogene Ölwannendichtfläche richten. Neuen Dichtungssatz
mit Fett an den Motorblock kleben, dabei auf richtigen Sitz
der Ölwannendichtung achten, Abb.77.
- Ölwanne einsetzen und mit
vorgeschriebenem Drehmoment, siehe Technische Daten,
festziehen. Ölablassschraube mit neuer Dichtung und
vorgeschriebenem Drehmoment einschrauben.
- Abstützung unter dem Getriebe
entfernen und Motor absenken.
- Kupplungsgehäuseabdeckung
anbringen und Gummipuffer Motorböcke mit vorgeschriebenem
Drehmoment am Achskörper anschrauben.
- Anlasser einbauen und
Anlasserkabel anschließen, Abb.78.
- Verteilerkappe anbauen und
Luftführung am Kühler anschrauben.
- Motoröl auffüllen und
Batterie-Massekabel anschließen. Motor laufen lassen und
Ölwanne auf Undichtigkeiten prüfen
|
Abb.76
Gummipuffer Motorböcke
abschrauben
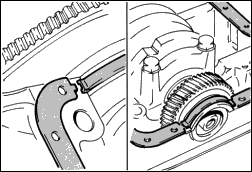
Abb.77
Ölwannendichtung montieren
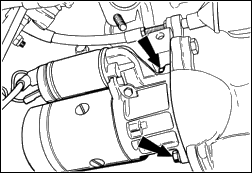
Abb.78 Anlasser
ausbauen
|
|
21 164
ZYLINDERKÖPFE AB- UND ANBAUEN |
|
KEIN
SPEZIALWERKZEUG ERFORDERLICH
Ansaugkopfschlüssel
.............................. |
21-092-A |
|
|
Abbauen
- Massekabel von der Batterie
abklemmen.
- Kühlmittel ablassen, dazu
unteren Kühlerschlauch vom Kühler und oberen Schlauch vom
Wasserauslassstutzen Motor lösen und Abziehen, Abb.79.
- Kühlmittelschläuche (3) vom
Zwischenstück des Zusatzluftschiebers abbauen, Abb.80.
- Unterdruckschlauch des
Bremskraftverstärkers vom Luftkammerstutzen abbauen.
- Unterdruckschläuche vom
Warmlaufregler und vom Drosselklappenstutzen abziehen, Abb.81.
|
Abb.79 Oberen
Kühlerschlauch lösen
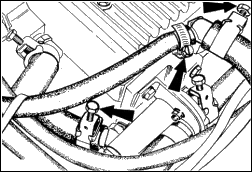
Abb.80
Kühlmittelschläuche am
Zusatzluftschieber
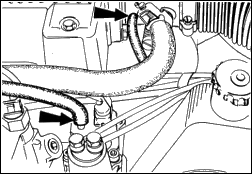
Abb.81
Unterdruckschläuche abziehen
|
- Stromkabel vom Geber
Fernthermometer, Thermozeitschalter, Warmlaufregler,
Zusatzluftschieber und Kaltstartventil abklemmen, Abb.82.
- Kraftstoffleitung vom
Kaltstartventil abschrauben, Abb.83, und Verbindungsschlauch
Ansauggeräuschdämpfer ausbauen.
- Gaszug am Drosselklappenhebel
aushängen und mit Halter abbauen (2 Schrauben), Abb.84.
|
Abb.82
Stromkabel abklemmen
A = Stecker Warmlaufregler
B = Thermozeitschalter
C = Geber Fernthermometer
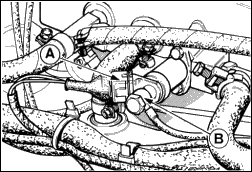
Abb.83
Einbaulage Kaltstartventil
A = Mehrfachstecker
B = Kraftstoffleitung
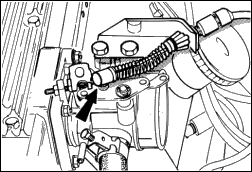
Abb.84 Gaszug
aushängen
|
- Motorbelüftungsschlauch mit
Ventil von Zylinderkopfhaube abziehen und Luftkammer vom
Ansaugkopf abmontieren (8 Schrauben), Abb.85.
- Kraftstoffleitungen von
Einspritzdüsen und Warmlaufregler abbauen und zur Seite
legen, Abb.86. Einspritzdüsen ausbauen.
Beachte: Düsen und Leitungen verschließen.
- Zündkabel von Zündspule und
Zündkerzen abziehen und Mehrfachstecker am Verteiler trennen.
Kurbelwellen-Riemenscheibe auf OT des 1. Zylinders drehen,
Klemmschraube unten am Verteiler lösen und Verteiler
ausbauen.
- Stromkabel von der
Lichtmaschine abklemmen. Lichtmaschine komplett mit Halter
abschrauben und Keilriemen abnehmen.
- Zündkerzen herausdrehen und
Zylinderkopfhauben abbauen. Kipphebelachsen mit Ölfangblechen
abmontieren, Abb.87. Stößelstangen entfernen.
Beachte: Stößelstangen mit Kipphebelachsen nicht
vertauschen.
|
Abb.85
Luftkammer abbauen
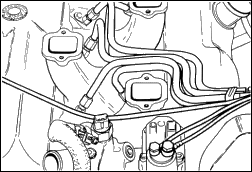
Abb.86
Kraftstoffleitungen abschrauben
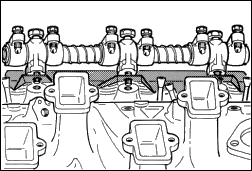
Abb.87
Kipphebelachse mit Ölfangblech
entfernen
|
- Bypass-Schlauch entfernen und
Ansaugkopf abschrauben. Falls erforderlich Ansaugkopf mit
einem Hebel von der Dichtung lösen, Abb.88. Nicht mit einem
Schraubendreher zwischen die Dichtflächen gehen.
- Auspuffrohre von
Auspuffkrümmern abschrauben (4 Muttern).
- Zylinderköpfe abbauen, dabei
Zylinderkopfschrauben in umgekehrter Reihenfolge wie beim
Anziehen lösen, siehe Anzugsreihenfolge Abb.90.
Anbauen
- Nach der Reinigung der
Dichtflächen (Zylinderblock - Zylinderköpfe - Ansaugkopf)
neue Zylinderkopfdichtungen über die Führungshülsen auf den
Zylinderblock auflegen, Abb.89.
Beachte: Zylinderkopf-Dichtungen sind mit "OBEN
VORN" gekennzeichnet.
- Zylinderköpfe aufsetzen und
Schrauben (an Kopf und Gewinde eingeölt) mit vorgeschriebenem
Drehmoment in drei Stufen nach Schema, Abb.90, festziehen,
siehe Technische Daten.
|
Abb.88
Ansaugkopf abbauen
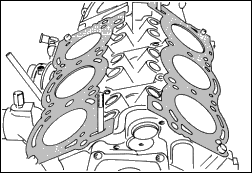
Abb.89
Zylinderkopfdichtungen auflegen
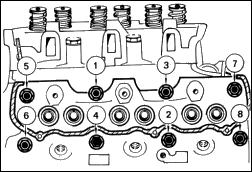
Abb.90
Anzugsreihenfolge Zylinderkopf
|
- Die vier Stoßstellen von
Zylinderblock, Zylinderköpfen und Ansaugkopf mit Dichtmasse
bestreichen, Abb.91, und neue Ansaugkopfdichtung auflegen.
- Ansaugkopf aufsetzen und mit
vorgeschriebenem Drehmoment in vier Stufen nach Schema,
Abb.92, festziehen. Bypass-Schlauch anbringen.
- Auspuffrohre an
Auspuffkrümmern montieren.
- Stößelstangen an beiden
Enden mit Motoröl benetzen und in die Ventilstößelpfannen
stellen. Ölfangbleche und Kipphebelachsen aufsetzen, Abb.93,
dabei Stellschrauben der Kipphebel in die
Stößelstangenpfannen führen. Schrauben der Kipphebelachsen
beidrehen und mit vorgeschriebenem Drehmoment anziehen.
- Ersten Zylinder auf OT stellen
und Verteiler einbauen.
- Ventilspiel einstellen, siehe Arbeitsposition
21 213.
|
Abb.91
Stoßflächen mit Dichtmasse
bestreichen
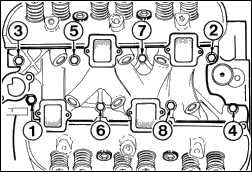
Abb.92
Anzugsreihenfolge Ansaugkopf
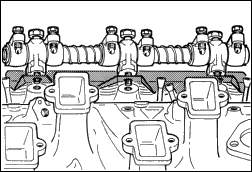
Abb.93
Kipphebelachse mit Ölfangblech
aufsetzen
|
- Zylinderkopfhauben montieren
und Zündkerzen einschrauben. Zündkabel auf Zündkerzen und
Zündspule aufstecken, Abb.94, Mehrfachstecker am Verteiler
verbinden.
- Lichtmaschine komplett mit
Halter anbauen und Mehrfachstecker anschließen.
- Keilriemen auflegen und
spannen, Abb.95.
Beachte: Die Riemenspannung sollte mit einem
Messwerkzeug, falls verfügbar, gemessen werden, siehe Technische
Daten. Andernfalls wird die erforderliche
Keilriemenspannung mit normalem Fingerdruck in der Mitte der
längsten Riemenspannweite gemessen. Gesamtspiel - 13 mm.
- Einspritzdüsen einschrauben
und Kraftstoffleitungen an Düsen und Warmlaufregler
befestigen, Abb.96.
|
Abb.94
Zündkabelanordnung (Zündfolge)

Abb.95
Keilriemen Lichtmaschine spannen
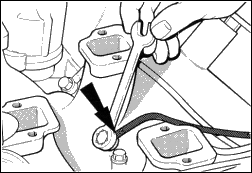
Abb.96
Kraftstoffleitung Einspritzdüse anbauen
|
- Luftkammer mit neuer Dichtung
an Ansaugkopf montieren und Motorbelüftungsschlauch an
Zylinderkopfhaube anbringen.
- Gaszug mit Halter am
Drosselklappenhebel anbauen, Abb.97.
- Kraftstoffleitung am
Kaltstartventil anschrauben und Verbindungsschlauch
Ansauggeräuschdämpfer montieren; dabei Einbaulage in Abb.102
beachten.
- Stromkabel an Geber
Fernthermometer, Thermozeitschalter, Warmlaufregler,
Zusatzluftschieber und Kaltstartventil anschließen, Abb.98.
Unterdruckschläuche am Drosselklappenstutzen und
Warmlaufregler aufstecken, Abb.99.
|
Abb.97 Gaszug
einbauen
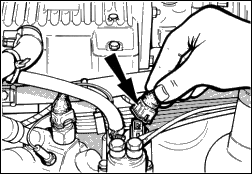
Abb.98 Stecker
Warmlaufregler montieren
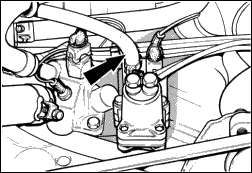
Abb.99
Unterdruckschlauch an Warmlauf-
Regler
|
- Unterdruckschlauch des
Bremskraftverstärkers am Luftkammerstutzen anbringen,
Abb.100, und Kühlmittelschläuche am Zwischenstück des
Zusatzluftschiebers befestigen.
- Oberen und unteren
Kühlerschlauch befestigen, Abb.101, und Kühlmittel
auffüllen.
- Massekabel der Batterie
anklemmen. Motor laufen lassen und auf Undichtigkeiten
überprüfen.
Nach dem Warmlaufen des Motors:
- Verbindungsschlauch
Ansauggeräuschdämpfer entfernen und Ausgleichbehälter vom
Halter abbauen.
- Zündkabel von Zündkerzen
abziehen und Zylinderkopfhauben abbauen.
- Zylinderkopf- und
Ansaugkopfschrauben (Spezialwerkzeug 21-092-A) mit
vorgeschriebenem Drehmoment nach Schema, Abb.90 und Abb.92,
nachziehen.
- Ventilspiel kontrollieren,
Zylinderkopfhauben montieren und Zündkabel aufstecken.
- Verbindungsschlauch
Ansauggeräuschdämpfer einbauen (Einbaulage in Abb.102
beachten) und Ausgleichbehälter befestigen.
- Zündzeitpunkt,
Leerlaufdrehzahl und CO-Gehalt einstellen.
|
Abb.100 Unterdruckschlauch Bremskraft-
Verstärker
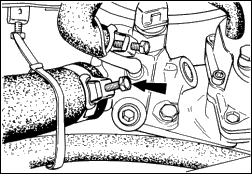
Abb.101 Oberen
Kühlerschlauch befestigen
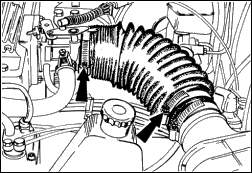
Abb.102
Verbindungsschlauch Ansaug-
Geräuschdämpfer
|
|
21 213
VENTILSPIEL EINSTELLEN |
|
KEIN
SPEZIALWERKZEUG ERFORDERLICH
|
|
- Massekabel von der Batterie
abklemmen.
- Verbindungsschlauch
Ansauggeräuschdämpfer ausbauen, Abb.103, und
Ausgleichbehälter vom Halter abbauen.
- Zündkabel von Zündkerzen
abziehen und Zylinderkopfhauben abschrauben.
- Ventilspiel einstellen,
Abb.104, dabei wie folgt verfahren:
Den Motor während der Ventilspieleinstellung nur in
Drehrichtung drehen und zunächst Kurbelwellen-Riemenscheibe
mit der Markierung auf die "0"-Marke des
Stirnraddeckels stellen.
Zur Erleichterung bei Beginn der Ventilspieleinstellung auf
der Riemenscheibe drei Kreidestriche anbringen, die eine
Unterteilung von 120° aufzeigen.
Wird die Riemenscheibe jetzt etwas hin- und hergedreht, so
überschneiden sich die Ventile am 1. oder 5. Zylinder, d.h.,
beide Kipphebel bzw. Stößelstangen bewegen sich
gegenläufig. Überschneiden sich die Ventile des 5.
Zylinders, so ist das Ventilspiel des 1. Zylinders
einzustellen. Wird die Riemenscheibe um 120° weitergedreht,
so überschneiden sich die Ventile des 3. Zylinders und das
Ventilspiel kann am 4. Zylinder eingestellt werden; usw.
entsprechend der Zündfolge, Abb.105. Einstellwerte siehe Technische
Daten.
5. Zyl. überschneidet - 1. Zyl. einstellen
3. Zyl. überschneidet - 4. Zyl. einstellen
6. Zyl. überschneidet - 2. Zyl. einstellen
1. Zyl. überschneidet - 5. Zyl. einstellen
4. Zyl. überschneidet - §. Zyl. einstellen
2. Zyl. überschneidet - 6. Zyl. einstellen
- Zylinderkopfhauben mit neuen
Dichtungen aufsetzen und festschrauben. Zündkabel aufstecken,
Abb.105.
- Ausgleichbehälter befestigen,
Verbindungsschlauch Ansauggeräuschdämpfer einbauen
(Einbaulage in Abb.103 beachten) und Batterie-Massekabel
anschließen.
|
Abb.103 Verbindungsschlauch Ansaug-
Geräuschdämpfer in Einbaulage
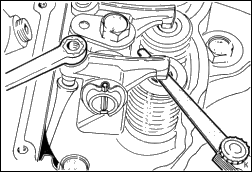
Abb.104 Ventilspiel
einstellen
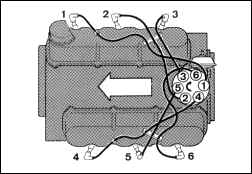
Abb.105
Zündkabelanordnung (Zündfolge)
|
|
21 238
ÖLABSCHIRMRINGE VENTILSCHAFT AUSWECHSELN |
|
ERFORDERLICHES
SPEZIALWERKZEUG:
Ventilfederspanner
................................
Ventilhalter ........................................... |
21-056
21-057 |
|
|
Ausbauen
- Massekabel von der Batterie
abklemmen.
- Verbindungsschlauch
Ansauggeräuschdämpfer ausbauen und Ausgleichbehälter vom
Halter abbauen, Abb.106.
- Schläuche und Kabel vom
Behälter der Scheibenwaschanlage entfernen und Behälter
herausnehmen. Halter von der Karosserie abschrauben (1
Schraube).
- Zündkabel von Zündkerzen
abziehen und Zylinderkopfhauben abschrauben.
- Zündkerzen herausschrauben,
Kipphebelachsen (6 Schrauben) mit Ölfangblechen abbauen,
Abb.107, und Stößelstangen entfernen.
Beachte: Stößelstangen und Kipphebelachsen nicht
vertauschen.
- Ventilhalter 21-057 in
Zündkerzenbohrungen einschrauben, gegen Ventilteller stellen
und Kontern. Ventilspanner 21-056 an Zylinderkopf montieren,
Abb.108.
- Ventilfeder mit
Spezialwerkzeug 21-056 herunterdrücken, Ventilkeile
entnehmen, Abb.109, und Ventilfeder entspannen.
Ventilfederteller mit Ventilfeder entfernen. Ölabschirmring
ausbauen.
Beachte: Bei der Demontage und Montage der Ventilfedern
ist unbedingt darauf zu achten, dass der Ventilschaft beim
Aus- und Einbau der Ventilkeile durch den heruntergedrückten
Ventilfederteller nicht beschädigt wird. Bei Beschädigungen
des Schaftes ist sonst keine Sicherheit für eine genügende
Abdichtung gegeben. Es erfolgen erhöhter Ölverbrauch und
Verschleißerscheinungen in der Ventilführung.
|
Abb.106 Ausgleichbehälter
ausbauen
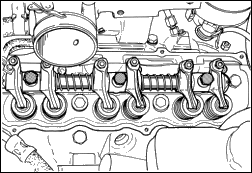
Abb.107
Kipphebelachse mit Ölfangblech
abbauen
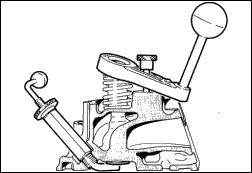
Abb.108 Abbau der
Ventilfeder mit Spezial-
Werkzeug 21-056 und 21-057
|
Einbauen
- Ventil-Keilnut mit Klebefolie
abkleben, neuen Ölabschirmring auf den Ventilschaft stecken,
Abb.110, und bis zur Anlage herunterschieben. Klebefolie von
Ventilschaft wieder entfernen. Ventilfeder und
Ventilfederteller aufsetzen, mit Spezialwerkzeug
zusammendrücken und Ventilkeile einsetzen. Auf richtigen Sitz
der Ventilkeile achten. Ventilfeder entspannen und
Spezialwerkzeug abbauen.
Beachte: Bei jedem Aus- und Einbau eines Ventils einen
neuen Ölabschirmring verwenden. Um eine Beschädigung der
Ölabschirmringe zu vermeiden, Ventil-Keilnuten mit Klebefolie
abkleben.
- Stößelstangen in die
Ventilstößelstangen stellen. Ölfangbleche und
Kipphebelachsen aufsetzen, dabei Stellschrauben der Kipphebel
in die Stößelstangenpfannen führen. Schrauben der
Kipphebelachsen beidrehen und mit vorgeschriebenem Drehmoment
anziehen.
- Ventilspiel einstellen( siehe Arbeitsposition
21 213). Zündkerzen einschrauben und Zylinderkopfhauben
anbauen.
- Zündkabel aufstecken und
Behälter der Scheibenwaschanlage einbauen. Schläuche und
Kabel anschließen.
- Ausgleichbehälter befestigen,
Verbindungsschlauch des Ansauggeräuschdämpfers einbauen
(Einbaulage in Abb.111 beachten) und Batterie-Massekabel
anschließen.
|
Abb.109
Ventilkeile ausbauen
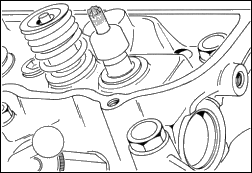
Abb.110
Ölabschirmring auf Ventilschaft
stecken
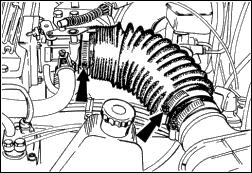
Abb.111
Verbindungsschlauch Ansaug-
Geräuschdämpfer in Einbaulage
|
TECHNISCHE DATEN
Motor allgemein
|
Kennzeichnungscode |
PRN |
Zündfolge |
1-4-2-5-3-6 |
Bohrung |
93,03
mm |
Hub |
68,50
mm |
Hubraum
effektiv |
2792
cm3 |
Hubraum
nach Steuerformel |
2772
cm3 |
Verdichtungsverhältnis |
9,2
: 1 |
Verdichtungsdruck
bei Anlasserdrehzahl |
11,5
bis 12,5 bar |
Mittlerer
Arbeitsdruck |
10,2
bar |
Leerlaufdrehzahl |
900
1/min |
Dauerdrehzahl
max. |
6100
1/min (Drehzahlbegrenzer) |
Motorleistung
(DIN) bei 5700 1/min |
118
kW (160 PS) |
Drehmoment
bei 4300 1/min |
221
Nm (22,5 mkp) |
Zylinderblock
|
Gusszeichen |
E |
Anzahl
der Hauptlager |
4 |
Zylinderbohrung
Ø
Standard Klasse 1 |
93,010
- 93,020 mm |
Zylinderbohrung
Ø
Klasse 2 |
93,020
- 93,030 mm |
Zylinderbohrung
Ø
Klasse 3 |
93,030
- 93,040 mm |
Zylinderbohrung
Ø
Klasse 4 |
93,040
- 93,050 mm |
Zylinderbohrung
Ø
Übergröße Klasse A |
93,520
- 93,530 mm |
Zylinderbohrung
Ø
Klasse B |
93,530
- 93,540 mm |
Zylinderbohrung
Ø
Klasse C |
93,540
- 93,550 mm |
Zylinderbohrung
Ø
Standard KD |
93,040
- 93,050 mm |
Zylinderbohrung
Ø
Übergröße 0,5 |
93,540
- 93,550 mm |
Zylinderbohrung
Ø
1,0 |
94,040
- 94,050 mm |
Spurlagerbreite |
22,610
- 22,660 mm |
Montierte
Hauptlagerschalen, senkrechter Innen-Ø Standard |
57,008
- 57,042 mm |
Untermaß 0,254 |
56,754
- 56,788 mm |
Hauptlager,
Grundbohrung-Ø
Standard |
60,620
- 60,640 mm |
Übergröße 0,38 |
61,000
- 61,020 mm |
Bohrung,
Nockenwellenlagerbüchsen-Ø
vorne |
45,025
- 45,060 mm |
mitte 1 |
44,645
- 44,680 mm |
mitte 2 |
44,265
- 44,300 mm |
hinten |
43,885
- 43,920 mm |
Kurbelwelle
|
Axialspiel |
0,080
- 0,280 mm |
Zahnflankenspiel |
0,17
- 0,27 mm |
Hauptlagerzapfen-Ø
Standard |
56,980
- 57,000 mm |
Untermaß 0,254 |
56,726
- 56,746 mm |
Spurlager,
Schulterbreite
Standard |
26,390
- 26,440 mm |
Übergröße |
26,871
- 26,821 mm |
Spurlagerbreite,
Bundlagerschale
Standard |
26,240
- 26,290 mm |
Übergröße |
26,621
- 26,671 mm |
Spiel
Lagerschale, Hauptlagerzapfen |
0,008
- 0,062 mm |
Pleuellagerzapfen-Ø
Standard |
53,980
- 54,000 mm |
Untermaß 0,254 |
53,726
- 53,746 mm |
Nockenwelle
|
Anzahl
Nockenwellenlager |
4 |
Antrieb |
Über
Zahnräder |
Dicke,
Nockenwellenhalteplatte
rot |
3,960
- 3,985 mm |
blau |
3,986
- 4,011 mm |
Hubhöhe
Nocken
Einlass |
6,700
mm |
Auslass |
6,600
mm |
Länge
Nocken (zwischen Ferse und
Spitze)
Einlass |
33,695
- 33,865 mm |
Auslass |
33,595
- 33,765 mm |
Nockenwellenlagerzapfen-Ø
vorne |
41,903
- 41,923 mm |
mitte 1 |
41,522
- 41,542 mm |
mitte 2 |
41,141
- 41,161 mm |
hinten |
40,760
- 40,780 mm |
Lagerbüchsen-Ø
vorne |
41,948
- 41,968 mm |
mitte 1 |
41,567
- 41,587 mm |
mitte 2 |
41,186
- 41,206 mm |
hinten |
40,805
- 40,825 mm |
Axialspiel |
0,02
- 0,10 mm |
Kolben
|
Kolben-Ø
Standard 1 |
92,972
- 92,982 mm |
2 |
92,982
- 92,992 mm |
3 |
92,992
- 93,002 mm |
4 |
93,002
- 93,012 mm |
KD Standard |
92,978
- 93,002 mm |
KD Übergröße 0,5 |
93,478
- 93,502 mm |
1,0 |
93,978
- 94,002 mm |
Kolbeneinbauspiel |
0,028
- 0,048 mm |
Kolbenring-Ringstoß
(eingebaut)
Kolbenring oben |
0,38
- 0,58 mm |
mitte |
0,38
- 0,58 mm |
unten |
0,38
- 1,40 mm |
Ringstoß
Position
oben |
150°
versetzt zum Stützfederringstoß |
mitte |
150°
versetzt zum Stützfederringstoß
entgegengesetzt zum Kolbenring oben |
Ölabstreifring
3-teilig
Zwischenring oben |
25
mm versetzt zum Stützfederringstoß |
Stützfeder |
Gegenüber
der markierten Kolbenseite |
Zwischenring unten |
25
mm versetzt zum Stützfederringstoß
entgegengesetzt zum Zwischenring oben |
Kolbenbolzen
|
Bolzen-Ø
rot |
23,994
- 23,997 mm |
blau |
23,997
- 24,000 mm |
Spiel
im Kolben (schwimmend) |
0,008
- 0,014 mm |
Überdeckung
Pleuel |
0,018
- 0,042 mm |
Pleuelstange
|
Bohrungs-Ø
(ohne
Lagerschalen)
großes Auge |
56,84
- 56,82 mm |
kleines Auge |
23,958
- 23,976 mm |
Senkrechter
Innen-Ø (Lagerschalen
montiert) Standard |
54,006
- 54,046 mm |
Untermaß 0,254 |
53,752
- 53,792 mm |
Spiel
Pleuelzapfen, Lagerschale |
0,006
- 0,064 mm |
Zylinderkopf
|
Gusszeichen |
EN |
Ventilsitzwinkel |
45° |
Ventilsitzbreite
Einlass/Auslass |
1,61
- 2,33 mm |
Oberer
Korrekturwinkel
(Prod.)
Einlass/Auslass |
18° |
Korrekturfräser für KD |
15° |
Unterer
Korrekturwinkel
(Prod.)
Einlass/Auslass |
60° |
Korrekturfräser für KD |
70° |
Schaftbohrung,
Einlass- und
Auslassventil
Standard |
8,063
- 8,088 mm |
Übergröße 0,2 |
8,263
- 8,288 mm |
0,4 |
8,463
- 8,488 mm |
Ventile
|
Ventilsteuerung |
Über
Stößelstangen und Kipphebel |
Ventilspiel
(kalt)
Einlass |
0,35
mm |
Auslass |
0,40
mm |
Einlassventil
öffnet |
24°
vor OT |
schließt |
72°
nach UT |
Auslassventil
öffnet |
73°
vor UT |
schließt |
25°
nach OT |
Ventilstößel-Ø |
22,190
- 22,202 mm |
Stößelspiel
im Gehäuse |
0,023
- 0,060 mm |
Einlassventil
|
Ventillänge |
105,0
- 106,2 mm |
Ventilteller-Ø |
41,850
- 42,240 mm |
Ventilschaft-Ø
Standard |
8,025
- 8,043 mm |
Übergröße 0,2 |
8,225
- 8,243 mm |
0,4 |
8,425
- 8,443 mm |
0,6 |
8,625
- 8,643 mm |
0,8 |
8,825
- 8,843 mm |
Spiel
Ventilschaftführung |
0,020
- 0,063 mm |
Ventilhub
bei 0,35 mm Ventilspiel |
9,388
- 9,463 mm |
Freie
Ventilfederlänge |
52,5
mm |
Federkraft
Ventil offen |
72,2
- 77,8 kp |
Ventil geschlossen |
38,2
- 42,0 kp |
Federhöhe
zusammengedrückt
Ventil offen |
31,04
mm |
Ventil geschlossen |
40,26 |
Auslassventil
|
Ventillänge |
105,2
- 106,2 mm |
Ventilteller-Ø |
35,830
- 36,210 mm |
Ventilschaft-Ø
Standard |
7,999
- 8,017 mm |
Übergröße 0,2 |
8,199
- 8,217 mm |
0,4 |
8,399
- 8,417 mm |
0,6 |
8,599
- 8,617 mm |
0,8 |
8,799
- 8,817 mm |
Spiel,
Ventilschaftführung |
0,046
- 0,089 mm |
Ventilhub
bei 0,40 mm Ventilspiel |
9,192
- 9,267 mm |
Freie
Ventilfederlänge |
52,5
mm |
Federkraft
Ventil offen |
72,2
- 77,8 kp |
Ventil geschlossen |
38,2
- 42,0 kp |
Federhöhe
zusammengedrückt
Ventil offen |
31,04
mm |
Ventil geschlossen |
40,26
mm |
Motorschmierung
|
Ölsorte |
HD-ÖL
(Ford-Super-Motoröl) |
Ford-Spezifikation |
SSM-2C9001-AA |
Viskosität
unter -12°C |
SAE
5W-20 |
unter 0°C |
SAE
5W-30 |
-23°C bis +32°C |
SAE
10W-30/40/50 |
über -12°C |
SAE
20W-40/50 |
Erstfüllmenge
mit Filter |
4,7
Ltr. |
Ölwechsel
ohne Filterwechsel |
4,0
Ltr. |
Ölwechsel
mit Filterwechsel |
4,25
Ltr. |
Mindest-Öldruck
bei
750/min (80°C) |
1,0
bar |
2000/min (80°C) |
2,8
bar |
Überdruckventil
öffnet
bei
(1000/min 80°C) |
4,0
- 4,7 bar |
Öldruck-Kontroll-Licht
leuchtet auf bei |
0,3
- 0,5 bar |
Ölpumpe,
Spiel Rotor - Gehäuse |
0,150
- 0,301 mm |
Spaltmaß
Innen - Außenrotor |
0,05
- 0,20 mm |
Axialspiel
Rotor - Dichtfläche |
0,028
- 0,104 mm |
Anzugsdrehmomente
|
Hauptlagerdeckel |
90
- 104 Nm (9,0 - 10,4 kpm) |
Pleuelschrauben |
26
- 33 Nm (2,6 - 3,3 kpm) |
Kurbelwellen-Riemenscheibe |
115
- 130 Nm (11,5 - 13,0 kpm) |
Nockenwellenzahnrad |
42
- 50 Nm (4,2 - 5,0 kpm) |
Nockenwellenhalteplatte |
17
- 21 Nm (1,7 - 2,1 kpm) |
Schwungrad |
65
- 70 Nm (6,5 - 7,0 kpm) |
Stirnraddeckel
an Zylinderblock |
17
- 21 Nm (1,7 - 2,1 kpm) |
Stirnraddeckel
an Zwischenplatte |
13
- 17 Nm (1,3 - 1,7 kpm) |
Zwischenplatte
an Zylinderblock |
17
- 21 Nm (1,7 - 2,1 kpm) |
Ölpumpe |
14
- 17 Nm (1,4 - 1,7 kpm) |
Ölpumpendeckel |
9
- 13 Nm (0,9 - 1,3 kpm) |
Kipphebelachse |
59
- 67 Nm (5,9 - 6,7 kpm) |
Ölwanne
1) |
4
- 7 Nm (0,4 - 0,7 kpm) |
2) |
7
- 10 Nm (0,7 - 1,0 kpm) |
Ölablassschraube |
21
- 28 Nm (2,1 - 2,8 kpm) |
Öldruckschalter |
12
- 15 Nm (1,2 - 1,5 kpm) |
Gewindehülse
- Ölkühler |
20
- 40 Nm (2,0 - 4,0 kpm) |
Zylinderkopf
1) |
39
- 54 Nm (3,9 - 5,4 kpm) |
2) |
54
- 69 Nm (5,4 - 6,9 kpm) |
nach 10 bis 20 Minuten Wartezeit 3) |
88
- 108 Nm (8,8 - 10,8 kpm) |
nach
Warmlaufen (15 Min bei 1000/min) nachziehen auf 4) |
88
- 108 Nm (8,8 - 10,8 kpm) |
Zylinderkopfhaube |
4
- 7 Nm (0,4 - 0,7 kpm) |
Ansaugkopf
1) |
4
- 8 Nm (0,4 - 0,8 kpm) |
2) |
8
- 15 Nm (0,8 - 1,5 kpm) |
3) |
15
- 21 Nm (1,5 - 2,1 kpm) |
4) |
21
- 25 Nm (2,1 - 2,5 kpm) |
nach
Warmlaufen (15 Min bei 1000/min) nachziehen auf 5) |
21
- 25 Nm (2,1 - 2,5 kpm) |
Luftkammer
an Ansaugkopf |
7
- 10 Nm (0,7 - 1,0 kpm) |
Zündkerzen |
30
- 40 Nm (3,0 - 4,0 kpm) |
Kupplungsdruckplatte
an Schwungrad |
17
- 21 Nm (1,7 - 2,1 kpm) |
Wasserpumpe |
7
- 10 Nm (0,7 - 1,0 kpm) |
Wasserstutzen
- Thermostatgehäuse |
7
- 10 Nm (0,7 - 1,0 kpm) |
Riemenscheibe
an Wasserpumpenflansch |
9
- 12 Nm (0,9 - 1,2 kpm) |
Lüfterkupplung
an Wasserpumpenflansch |
20
- 50 Nm (2,0 - 5,0 kpm) |
Lüfter
an Lüfterkupplung |
8
- 10 Nm (0,8 - 1,0 kpm) |
Kupplungsgehäuse
an Motor |
30
- 37 Nm (3,0 - 3,7 kpm) |
|