21 Motor "A" - 1,3 Liter HC OHV-I4
Inhalt
-
Allgemeines
-
Prüfung
und Einstellung
-
Spezialwerkzeuge
-
Technische
Daten - Motor A, 1,3 Liter HC OHV-I4
-
Technische Daten - Motor
B, 1,6 Liter HC OHV-I4 (72/88 PS), 2,0 Liter HC OHV-I4
-
Technische Daten - Motor
C, 2,3 Liter HC OHV-V6
-
Technische Daten - Motor
F, 3,0 Liter HC OHV-V6 Essex
Arbeitspositionen
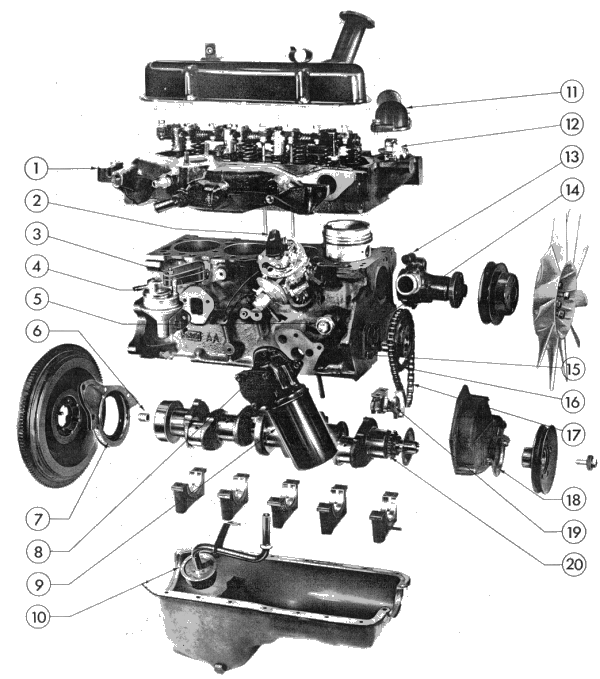
Abb.23 "A"-Motor zerlegt
1 =
Ansaugkrümmer
2 = Zündverteiler
3 =
Ölabscheider
4 = Kraftstoffpumpe
5 =
Öldruckschalter
6 = Lager - Getriebeantriebswelle
7 = Kurbelwellen
Dichtringträger 8 =
Ölpumpe
9 =
Ölfilter
10 = Ölpumpensieb mit Saugrohr
11 =
Wasserauslassstutzen
12 = Thermostat
13 =
Wasserpumpe
14 = Nockenwelle
15 =
Nockenwellen-Halteplatte
16 = Nockenwellenrad
17 =
Steuerkette
18 = Stirnraddeckel mit Dichtring
19 =
Kettenspanner
20 = Kurbelwellenrad
Ölkreislauf,
Abb.24
Die Ölpumpe saugt das in der
Ölwanne befindliche Öl über ein Sieb an und drückt es in den
Hauptstrom-Ölfilter. Durch die Mittelachse der Ölfilterpatrone
gelangt das gefilterte Öl über einen kurzen Kanal (rechte
Motorseite) zum Öldruckschalter und über eine Querbohrung zum
Hauptölkanal (linke Motorseite). Die Kurbelwellenlager stehen in
direkter Verbindung mit dem Hauptölkanal, wobei die
Nockenwellenlager wiederum mit dem vorderen, mittleren und
hinteren Kurbelwellenlager in Verbindung stehen. Die
Pleuellagerzapfen der Kurbelwelle werden jeweils vom
nächstgelegenen Kurbelwellenlager durch schräge Bohrungen mit
Öl versorgt. Die Pleuel haben im Pleuelfuß eine Spritzbohrung,
welche die Kolbenbolzen und die unbelastete Seite der Zylinder mit
Öl versorgt. Steuerkette und Stirnräder werden ebenfalls über
eine Spritzbohrung geölt. Der vordere Lagerzapfen der Nockenwelle
hat in der Mitte eine gefräste Fläche, über die Drucköl
schubweise (durch eine Bohrung im Zylinderblock und Zylinderkopf)
zur Kipphebelwelle gelangt.
|
Abb.24 Ölkreislauf
|
Geschlossene Motordurchlüftung,
Abb.25
Die Durchlüftung des
Kurbelgehäuses ist abhängig von der angesaugten Luftmenge des
laufenden Motors und dem Durchlass des Regulierventils. Die
Frischluft gelangt über den Öleinfüllstutzen in die
Zylinderkopfhaube, durchströmt das Kurbelgehäuse und wird an der
rechten Motorseite über das Regulierventil im Ölabscheider vom
laufenden Motor angesaugt und mit dem Vergasergemisch verbrannt.
Das Regulierventil regelt den Luftdurchsatz in Abhängigkeit vom
Belastungszustand des Motors.
Das Regulierventil wird in Intervallen, wie unter "Wartung"
beschrieben, mit einem Reinigungsmittel gereinigt und nach dem
Ausblasen wieder in den Ölabscheider eingesetzt.
|
Abb.25 Geschlossene Motordurchlüftung
|
ARBEITSPOSITIONEN
|
21 134 8
Motor zerlegen und
zusammenbauen |
|
ERFORDERLICHE
SPEZIALWERKZEUGE
Universalwelle |
............................................... |
21-023 |
Zentrierdorn |
................................................. |
21-029 |
Einpressdorn |
................................................. |
21-030 |
Motor-Aufspannvorrichtung |
............................. |
21-031 |
Abzieher,
Kurbelwellen-Zahnrad |
..................... |
21-035 |
Auszieher,
Nadellager |
.................................... |
21-036 |
Zentrierdorn |
................................................. |
21-044 |
Ölfilterschlüssel |
....................................... |
GV-6883-A |
Zentrierbolzen |
........................................... |
P-4063-A |
Einbaudorn |
................................... |
G2-6362/P-6161-A |
|
|
|
Zerlegen
- Motor mit Aufspannvorrichtung
21-023/21-031 am Montageständer, Abb.26, befestigen.
- Kupplungsdruckplatte (6
Schrauben) und Reibscheibe von der Schwungscheibe abbauen,
Abb.27.
- Motoröl ablassen, Ölfilter
mit Ölfilterschlüssel GV-6883-A, Abb.28, abschrauben.
- Zündkerzenstecker abziehen
und Verteilerkappe mit Zündkabel abnehmen. Zündkerzen
ausbauen.
- Unterdruckleitung
Zündverteiler vom Vergaser abziehen.
|
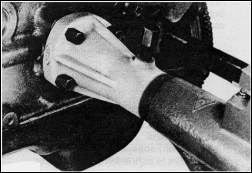
Abb.26 Motor-Aufspannvorrichtung
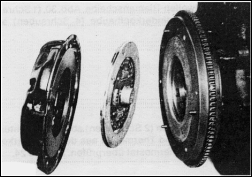
Abb.27 Kupplungsdruckplatte mit
Reibscheibe und Schwungscheibe
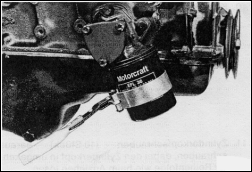
Abb.28 Ölfilter abbauen
|
- Kraftstoffleitung vom Vergaser
abbauen und Schlauch Motorbelüftung mit Regulierventil vom
Ölabscheider abziehen.
- Verstelllasche Lichtmaschine
lösen. Keilriemen abnehmen und Lichtmaschine mit Halter (3
Schrauben) abbauen, Abb.29. Lüfter mit Riemenscheibe (4
Schrauben) abschrauben.
- Kurbelwellen-Riemenscheibe,
Abb.30, (1 Schraube) und Zylinderkopfhaube (4 Schrauben)
abbauen.
- Wasserstutzen (2 Schrauben)
abbauen. Dichtung entfernen und Thermostat aus dem
Zylinderkopf nehmen. Thermostat überprüfen, siehe Gruppe
24.
- Kipphebelachse (4 Schrauben),
Abb.31, abschrauben und Stößelstangen entfernen. Stößelstangen
beim Aus- und Einbau nicht vertauschen!
- Zylinderkopfschrauben (10
Stück) herausschrauben, dabei den Zylinderkopf in umgekehrter
Reihenfolge wie beim Anziehen lösen.
|
Abb.29 Befestigung Lichtmaschine
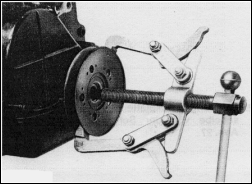
Abb.30 Kurbelwellen-Riemenscheibe mit
handelsüblichem Werkzeug
abziehen
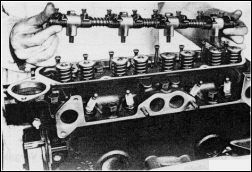
Abb.31 Kipphebelachse abbauen
|
- Zylinderkopf komplett mit
Ansaugkrümmer und Auspuffkrümmer abheben.
- Kraftstoffpumpe (2 Schrauben)
mit Dichtplatte, Abb.32, abschrauben.
- Schraube vom Ölabscheider
herausdrehen. Ölabscheider mit einem Schraubenzieher, Abb.33,
aus dem Motorblock drücken.
- Zündverteiler (1 Schraube)
aus- und Ölpumpe (3 Schrauben) abbauen. Öldruckschalter
abschrauben.
- Ölwanne nach unten, Abb.34,
abbauen, damit kein Ölschlamm und keine Abriebteile in den
Motor gelangen.
- Die Kolben auf halbe Hubhöhe
stellen und Ölkohlekranz am oberen Zylinderrand mit einem
Schaber entfernen, dabei nicht die Kolbenringlaufzone
berühren.
|
Abb.32 Kraftstoffpumpe abbauen
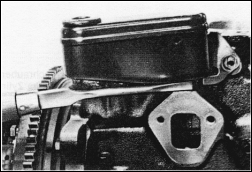
Abb.33 Ölabscheider mit Hilfe eines
Schraubenziehers ausbauen
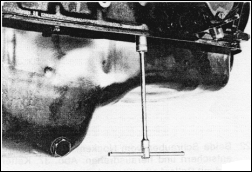
Abb.34 Ölwanne abschrauben
|
- Den Motor schwenken, dabei
vorher eine größere Ölauffangwanne unterstellen, um
Restbestände an Öl, der entfernten Ölkohle und
Kühlflüssigkeit aufzufangen.
- Wasserpumpe (3 Schrauben),
Abb.35, abbauen, Stirnraddeckel (4 Schrauben) abschrauben und
Ölschleuderblech von der Kurbelwelle, Abb.36, abnehmen.
- Ölpumpen-Saugrohr (1
Schraube) abschrauben, hin und her bewegen und dabei aus dem
Zylinderblock ziehen.
- Spannarm vom Stift des
vorderen Hauptlagerdeckels abziehen und den entspannten
Kettenspanner (2 Schrauben) abschrauben.
- Beide Schrauben vom
Nockenwellen-Kettenrad entsichern und herausdrehen, Abb.37.
Kettenrad mit Rollenkette (Steuerkette) abnehmen.
|
Abb.35 Wasserpumpe abbauen
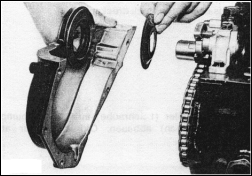
Abb.36 Stirnraddeckel mit
Ölschleuderblech
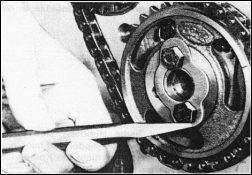
Abb.37 Nockenwellen-Kettenrad
entsichern
|
- Die beiden Schrauben der
Nockenwellen-Halteplatte entsichern und herausdrehen, Abb.38.
Halteplatte entfernen.
- Nockenwelle zum Stirnraddeckel
hin herausziehen, dabei vorher die Nockenwelle um 360°
drehen, damit die Stößel in OT-Stellung sind. Stößel
herausnehmen. Stößel beim Aus- und Einbau nicht
vertauschen.
- Führungslager-Antriebswelle
mit Spezialwerkzeug 21-036 aus der Kurbelwelle, Abb.39,
ziehen.
- Kurbelwellen-Kettenrad mit
Spezialwerkzeug 21-035 abziehen, Abb.40.
|
Abb.38 Nockenwellen-Halteplatte
abschrauben
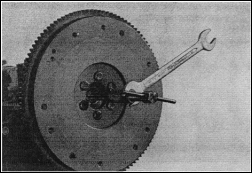
Abb.39 Führungslager-Antriebswelle
herausziehen
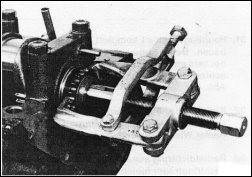
Abb.40 Kurbelwellen-Kettenrad abziehen
|
- Die Bezeichnung aller Pleuel-
und Hauptlagerdeckel, Abb.41, für den späteren Wiedereinbau
überprüfen.
- Pleuellagerdeckel einzeln mit
Lagerschale abbauen. Kolben mit Pleuelstange und Lagerschalen
zusammen aus dem Motor drücken. Sollten vor Einbau der Kolben
die Pleuelstangen-Lagerschalen entnommen werden, sind diese
entsprechend der Pleuelstange zwecks eventuellem Wiedereinbau
zu kennzeichnen.
- Schwungscheibe (6 Schrauben)
abschrauben und Zwischenplatte entnehmen.
- Radial-Dichtringträger
hinten, Abb.42, abbauen (4 Schrauben).
- Hauptlagerdeckel komplett mit
Lagerschale abbauen. Beim Abbau des mittleren
Hauptlagerdeckels auf den Sitz der beiden Anlauf-Halbringe
achten und dementsprechend kennzeichnen, Abb.43.
- Kurbelwelle aus dem
Zylinderblock heben. Lagerschalen herausnehmen und zwecks
eventueller Wiederverwendung kennzeichnen.
- Radialdichtring aus dem
Stirnraddeckel und dem Dichtringträger hinten entfernen.
|
Abb.41 Bezeichnung, Pleuel und
Hauptlagerdeckel
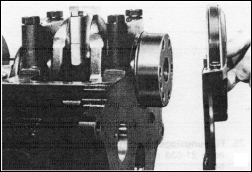
Abb.42 Radial-Dichtringträger hinten
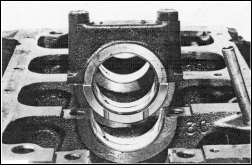
Abb.43 Anlauf-Halbring
|
Zusammenbauen
Laufzeit, eventueller
Motorschadensumfang sowie die beabsichtigte weitere Verwendung von
Einzelteilen bestimmen Grad und Art der Reinigung, die dem
Zusammenbau vorausgehen muss. Hierbei ist besonders der
Zylinderblock mit seinen Ecken, Winkeln und Bohrungen betroffen.
Alle Verschlussstopfen und Deckel gegebenenfalls entfernen und
deren Sitze mit geeigneten Reinigungsmitteln und Werkzeugen
(Bürsten, Schaber) reinigen. Besonders die Ölkanäle, z.B. von
Zylinderblock, Zylinderkopf usw. müssen frei von Schmutz und
Spänen sein, Abb.44. Falls eingepresste Verschlussdeckel und
Wasserstopfen entfernt wurden, so sind diese, wie auch alle
anderen Dichtungen, grundsätzlich bei jeder Motorreparatur durch
neue zu ersetzen.
Wird der Motorblock neu vermessen (Lagerspiele, Kolbenlaufspiele),
siehe Allgemeines.
|
Abb.44 Ölkreislauf
|
Kurbelwelle
Lagern
Grundbohrung im Zylinderblock
Die Grundbohrung im Zylinderblock kann entweder Standardmaß oder
0,38 mm Übergröße haben. Bei einer Standardmaß-Grundbohrung
ist keine Kennzeichnung vorhanden, während bei einer Bohrung mit
Übergröße die Lagerdeckel mit weißen Farbpunkten
gekennzeichnet sind, Abb.45.
|
Abb.45 Farbmarkierung Lagerdeckel
|
Hauptlagerzapfen der Kurbelwelle
Die Hauptlagerzapfen der Kurbelwelle können Standard-Durchmesser
und (auch in neuen Motoren) 0,25 mm Untermaß haben. Die
Lagerzapfen sind bei Standard-Durchmesser ohne Kennzeichnung, bei
Untermaß ist das 1. Gegengewicht mit einem grünen Farbstrich
gekennzeichnet, Abb.46.
|
Abb.46 Farbmarkierung Hauptlagerzapfen
|
Pleuellagerzapfen der Kurbelwelle
Die Pleuellagerzapfen der Kurbelwelle können ebenfalls
Standard-Durchmesser und (auch in neuen Motoren) 0,25 mm Untermaß
haben. Die Lagerzapfen sind bei Standard-Durchmesser ohne
Kennzeichnung, bei Untermaß ist an der 1. Wange zum Pleuelzapfen
ein grüner Farbpunkt, Abb.47.
|
Abb.47 Farbmarkierung Pleuellagerzapfen
|
Lagerschalen
Die Standard Haupt- und Pleuellagerschalen der Kurbelwelle
erhalten keine Farbkennzeichnung. Übergröße-Lagerschalen sind
auf der Rückseite entsprechend beschriftet (siehe
Ersatzteilkatalog). Das grüne Farbzeichen befindet sich seitlich
an der Außenkante, Abb.48.
Bei der Auswahl von neuen Lagerschalen muss in jedem Fall die
Zugehörigkeit im Ersatzteilkatalog überprüft und zusätzlich
ausgemessen werden!
Um in den Grenzen des vorgeschriebenen Lagerspieles, siehe Technische
Daten, zu bleiben, müssen Lagerzapfen und Bohrungen mit
Lagerschalen einzeln vermessen werden.
|
Abb.48 Lagerschale mit Farbmarkierung
|
- Radialdichtring des
Dichtringträgers mit Spezialwerkzeug 21-030 und des
Stirnraddeckels mit Spezialwerkzeug G2-6362/P-6161-A
einpressen, Abb.49.
- Neues Führungslager
Antriebswelle mit Spezialwerkzeug 21-044, Abb.50, in die
Kurbelwelle einpressen. Kurbelwellen-Kettenrad aufpressen.
- Stößel mit Öl benetzen und
in den Zylinderblock einsetzen.
- Nockenwellenlager, Nockenwelle
und Halteplatte mit Öl benetzen. Anschließend Nockenwelle
vom vorderen Lager her einbauen. Halteplatte anschrauben und
Schrauben mit Sicherungsblech sichern, Abb.51.
- Block-Hauptlagerschalen
trocken in den Zylinderblock einsetzen, dann mit Motoröl
benetzen und die Kurbelwelle einlegen.
- Hauptlagerdeckel komplett mit
eingeölten Lagerschalen aufsetzen. Im Führungslagerdeckel
darauf achten, dass die beiden Anlaufringe eingelegt sind.
Der Pfeil auf den Hauptlagerdeckeln muss in Richtung
Riemenscheibe zeigen, Abb.52.
- Schrauben der Lagerdeckel
gleichmäßig mit vorgeschriebenem Drehmoment festdrehen.
|
Abb.49 Radialdichtringe einpressen
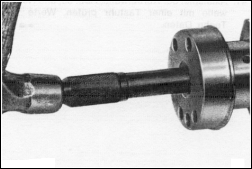
Abb.50 Führungslager Antriebswelle
einpressen
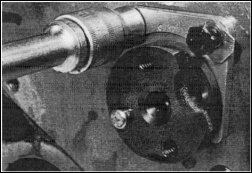
Abb.51 Nockenwellen-Halteplatte
anschrauben
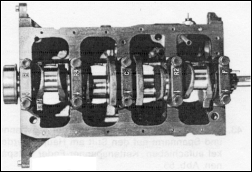
Abb.52 Montageanordnung
Hauptlagerdeckel
|
- Axialspiel der Kurbelwelle,
Abb.53, und Nockenwelle mit einer Tastuhr prüfen. Werte siehe
Technische Daten.
- Nockenwellen-Kettenrad mit
Steuerkette anbauen, darauf achten, dass die Markierung der
Kettenräder, Abb.54, gegeneinander stehen. Schrauben mit
vorgeschriebenem Drehmoment festdrehen und sichern.
- Kettenspanner anschrauben.
Feder vorspannen und Spannarm auf dem Stift am
Hauptlagerdeckel aufschieben. Kettenspanner-Feder entspannen,
Abb.55.
|
Abb.53 Axialspiel der Kurbelwelle
prüfen
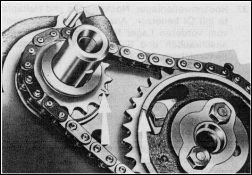
Abb.54 Markierung der Kettenräder
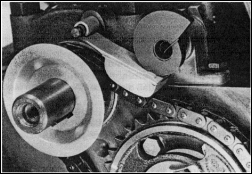
Abb.55 Montierter Kettenspanner
|
- Ölschleuderblech aufschieben,
Stirnraddeckel mit neuem Radialdichtring (Dichtlippe leicht
eingeölt oder eingefettet) in Verbindung mit der
Kurbelwellen-Riemenscheibe zentrieren, Abb.56.
- Stirnraddeckel und
Kurbelwellen-Riemenscheibe mit vorgeschriebenem Drehmoment
anziehen.
- Dichtringträger hinten mit
neuem Radialdichtring (Dichtlippe leicht eingeölt oder
eingefettet) mittels Spezialwerkzeug 21-029 zentrieren,
Abb.57. Dichtringträger mit vorgeschriebenem Drehmoment
festdrehen.
- Den Motor schwenken und
Zwischenplatte auflegen. Schwungscheibe anbauen, Abb.58, und
mit vorgeschriebenem Drehmoment festziehen.
|
Abb.56 Stirnraddeckel mit Kurbelwellen-
Riemenscheibe zentrieren
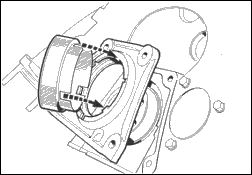
Abb.57 Hinteren Dichtringträger mit
Spezialwerkzeug 21-029
montieren
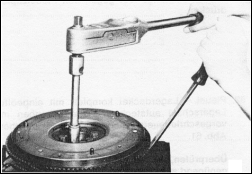
Abb.58 Schwungscheibe anbauen
|
- Reibscheibe mit
Spezialwerkzeug 21-044 zentrieren, Abb.59. Druckplatte auf die
Passstifte aufsetzen und mit vorgeschriebenem Drehmoment
festziehen.
- Kolben und Zylinderbahnen mit
Motoröl benetzen. Kolbenringstöße auf größtmöglichen
Abstand zueinander verdrehen.
- Kolbenringe mit
handelsüblichem Werkzeug (Spannband) zusammenziehen, Abb.60.
Kolben mit einem Hammerstiel in den Zylinder drücken, dabei
das Pleuel mit der hand auf den Pleuelzapfen führen.
Bei der Montage muss die Frontmarkierung des Kolbens
(Pfeil, Kerbe, usw.) in Richtung Stirndeckel zeigen, Abb.60.
- Lagerschale Pleuelstange
einlegen, einölen und Pleuelstange fest gegen den
Pleuelzapfen drücken.
- Pleuel Lagerdeckel komplett
mit eingeölter Lagerschale aufstecken. Pleuelschrauben mit
vorgeschriebenem Drehmoment festdrehen, Abb.61.
Überprüfen, ob das Pleuel auf dem Pleuelzapfen genügend
axiales Spiel hat.
|
Abb.59 Kupplungsreibscheibe mit
Werkzeug 21-044 zentrieren
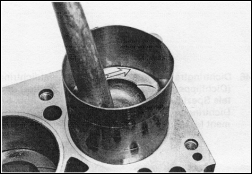
Abb.60 Kolben mit Spannband
einbauen
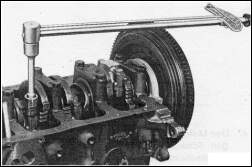
Abb.61 Pleuelschrauben mit vorge-
schriebenem Drehmoment
festziehen
|
- Ölpumpen-Saugrohr mit
Metallverbinder (Loctite) bestreichen und einpressen. Schraube
mit Drehmoment anziehen.
- Gummidichtung in die Nut des
hinteren Dichtringträgers und in den Stirndeckel einsetzen.
Zylinderblockdichtfläche am Stoß vom Stirndeckel und
Dichtringträger hinten mit Dichtmasse bestreichen.
Ölwannendichtung auflegen und die Nasen der Korkdichtung
unter die Aussparung in der Gummidichtung schieben, Abb.62.
- Ölwanne aufsetzen und
Schrauben mit vorgeschriebenem Drehmoment in zwei Stufen
anziehen.
- Den Motor in Einbaulage
Ölabscheider drehen. Ölabscheider bis Anschlag einsetzen und
mit Schraube sichern.
- Öldruckschalter mit
vorgeschriebenem Drehmoment festdrehen.
- Wasserpumpe anbauen, Abb.63.
dabei die Schraube der Lichtmaschinen- Verstellasche nur
handfest beiziehen.
- Motor auf OT des 1. Zylinders
stellen und Zündverteiler einbauen, siehe Gruppe
22.
- Ölpumpe mit Dichtung
montieren und Schrauben mit vorgeschriebenem Drehmoment
festdrehen, Abb.64.
Bei Verwendung einer überholten oder neuen Ölpumpe ist
diese vor dem Einbau von hand durchzudrehen und mit Motoröl
zu füllen.
|
Abb.62 Montage der Ölwannendichtung
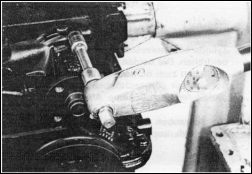
Abb.63 Wasserpumpe anschrauben
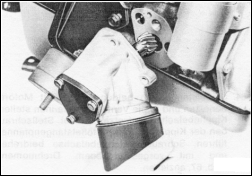
Abb.64 Ölpumpe montieren
|
- Ölfilterpatrone aufschrauben,
bis die Gummidichtung mit dem Gehäuse Kontakt hat, dann noch
eine 3/4-Umdrehung festdrehen. Gummidichtung vor der Montage
mit Motoröl benetzen.
- Spezialwerkzeug P-4063-A, wie
in Abb.65 gezeigt, eindrehen und Zylinderkopfdichtung richtig
auflegen.
- Zylinderkopf aufsetzen und die
Schrauben etwas beidrehen. Die beiden Zentrierbolzen gegen die
restlichen zwei Schrauben tauschen. Den Zylinderkopf mit
vorgeschriebenem Drehmoment in drei Stufen nach Schema,
Abb.66, festdrehen.
Die Schrauben haben entsprechend der Höhe des
Zylinderkopfes unterschiedliche Längen.
- Stößelstangen an beiden
Enden mit Motoröl benetzen und in die Ventilstößelpfannen
stellen. Kipphebelachse aufsetzen, dabei Stellschrauben der
Kipphebel in die Stößelstangenpfannen führen.
Schrauben-Kipphebelachse beidrehen und mit vorgeschriebenem
Drehmoment, Abb.67, anziehen.
|
Abb.65 Zylinderkopf mit Hilfe von
Zentrierbolzen montieren
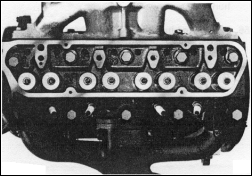
Abb.66 Anzugsreihenfolge für
Zylinderkopf
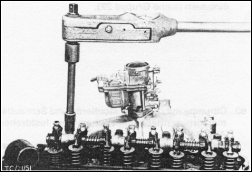
Abb.67 Kipphebelachse anziehen
|
- Thermostat in den Zylinderkopf
einsetzen, Abb.68. Dichtung auflegen und Wasserstutzen
anschrauben.
- Ventilspiel einstellen, siehe
Position 21 213, und Zylinderkopfhaube montieren.
- Lichtmaschine mit Halter
anbauen. Lüfter mit Riemenscheibe an Wasserpumpe montieren.
- Keilriemen auflegen und so mit
der Lichtmaschine spannen, dass sich der Keilriemen zwischen
Lichtmaschine und Lüfter 13 mm durchdrücken lässt.
- Kraftstoffpumpe mit
Dichtplatte anbauen. Schrauben mit Drehmoment festdrehen,
Abb.69.
- Kraftstoffleitung an Vergaser
anschließen und das Regulierventil der Motorbelüftung in den
Ölabscheider stecken.
- Zündkerzen mit
vorgeschriebenem Drehmoment festziehen. Verteilerkappe
aufsetzen und Zündkabel in gezeigter Anordnung, Abb.70, auf
die Zündkerzen stecken. Unterdruckleitung am Vergaser
anschließen.
- Ölablassschraube mit neuer
Dichtung und vorgeschriebenem Drehmoment festziehen.
Bei jedem Ölwechsel und Lösen der Ölablassschraube ist
ein neuer Dichtring entsprechend der Kundendienstanweisung zu
verwenden.
- Ölmessstab einschieben und
Motor vom Montageständer abbauen.
|
Abb.68 Einbaulage Thermostat
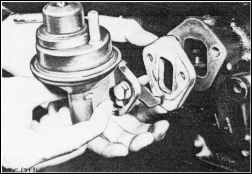
Abb.69 Kraftstoffpumpe montieren
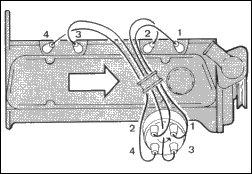
Abb.70 Zündkabelanordnung (Zündfolge)
|
|
21 163
Zylinderkopf ab- und anbauen |
|
KEIN
SPEZIALWERKZEUG ERFORDERLICH
|
|
Abbauen
- Batterie - Massekabel abklemmen
und Schutzpappe - Ölwanne abmontieren (4 Schrauben, 4 Clipse).
Kühlflüssigkeit ablassen, dabei Kühlerschlauch unten vom
Kühler, Abb.227, und oben vom Wasserauslassstutzen - Motor
entfernen.
- Ansauggeräuschdämpfer,
Kraftstoffleitung von Vergaser und Schlauch - Motorbelüftung vom
Ölabscheider abmontieren.
- Halter-Gasgestänge mit
eingehangenem Gaszug von Ansaugrohr abschrauben (2 Schrauben),
Abb.228. Betätigungszug - Startervergaser vom Vergaser entfernen.
- Unterdruckleitung vom Vergaser
abziehen. Heißwasserschlauch und Halter - Verlängerung - Rohr -
Ölmessstab (1 Schraube) von Ansaugkrümmer abbauen.
- Kabel von Geber - Fernthermometer,
Zündkabel von Zündkerzen und Zündspule entfernen.
Verteilerkappe und Verteilerfinger abnehmen.
- Wasserauslassstutzen -
Zylinderkopf abschrauben (2 Schrauben) und Thermostat
herausnehmen, Abb.229. Auspuffrohr von Auspuffkrümmer abschrauben
(2 Muttern).
|
Abb.227 Kühlerschlauch vom Kühler
entfernen
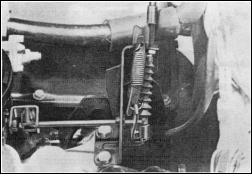
Abb.228 Halter - Gasgestänge abbauen
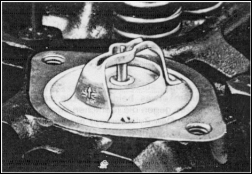
Abb.229 Einbaulage - Thermostat
|
- Zylinderkopfhaube (4 Schrauben)
und Zündkerzen entfernen. Kipphebelachse abschrauben (4
Schrauben), Abb.230. Stößelstangen herausnehmen und Zylinderkopf
(10 Schrauben) abbauen, dabei Zylinderkopfschrauben in umgekehrter
Reihenfolge wie beim Festdrehen lösen, siehe Anzugsreihenfolge
Abb.232.
Stößelstangen beim Aus- und Einbau nicht vertauschen.
Anbauen
- Nach Reinigen der Dichtflächen
(Zylinderkopf - Zylinderblock) Zylinderkopf - Zentrierbolzen in
den Zylinderblock schrauben und neue Zylinderkopf-Dichtung
auflegen.
- Zylinderkopf aufsetzen, Abb.231,
und die Schrauben etwas beidrehen. Die beiden Zentrierbolzen gegen
die restlichen zwei Schrauben tauschen. Den Zylinderkopf mit
vorgeschriebenem Drehmoment in drei Stufen nach Schema, Abb.232,
festdrehen.
Die Schrauben haben entsprechend der Höhe des Zylinderkopfes
unterschiedliche Längen.
|
Abb.230 Kipphebelachse entfernen
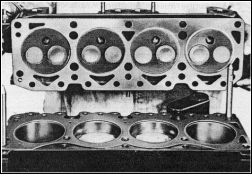
Abb.231 Zylinderkopf mit Hilfe von
Zentrierbolzen aufsetzen
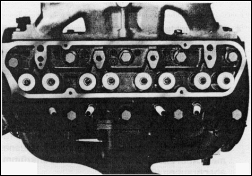
Abb.232 Anzugsreihenfolge Zylinderkopf
|
- Stößelstangen an beiden Enden
mit Motoröl benetzen und in die Ventilstößelpfannen stellen.
Kipphebelachse aufsetzen, dabei Stellschrauben der Kipphebel in
die Stößelstangenpfannen führen, Schrauben - Kipphebelachse
beidrehen und mit vorgeschriebenem Drehmoment anziehen, Abb.233.
- Ventilspiel einstellen, siehe Position
21 213. Zündkerzen einschrauben und Zylinderkopfhaube
anbringen.
- Thermostat einsetzen, Abb.234, und
Wasserauslassstutzen anschrauben. Auspuffrohr an Auspuffkrümmer
montieren.
- Kabel auf Geber - Fernthermometer,
Zündkabel auf Zündkerzen und Zündspule stecken. Verteilerfinger
und Verteilerkappe montieren.
- Unterdruckleitung am Vergaser
anschließen, Halter - Verlängerung - Rohr - Ölmessstab und
Heißwasserschlauch an Ansaugkrümmer anbringen.
- Halter - Gasgestänge mit
eingebautem Gaszug am Ansaugrohr anschrauben, Abb.235.
Betätigungszug - Startervergaser am Vergaser befestigen.
- Schlauch - Motorbelüftung an
Ölabscheider und Kraftstoffleitung an Vergaser anbauen.
|
Abb.233 Kipphebelachse mit vorge-
schriebenem Drehmoment
festziehen
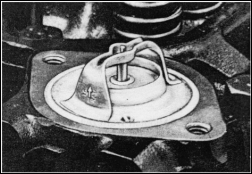
Abb.234 Einbaulage - Thermostat
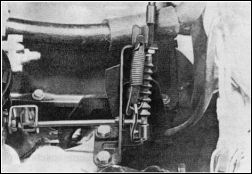
Abb.235 Halter - Gasgestänge montieren
|
- Kühlerschläuche anschließen und
Kühlmittel einfüllen.
Batterie - Massekabel anklemmen und Schutzpappe - Ölwanne
montieren.
- Motoreinstellung nach Vorschrift
bei Betriebstemperatur vornehmen. Schließwinkel, Zündzeitpunkt,
Abb.236, Leerlauf und CO-Gehalt einstellen.
- Nachdem die Einstellarbeiten bei
betriebswarmem Motor erledigt sind, Zündkabel von Zündkerzen
abziehen und Zylinderkopfhaube abbauen.
- Nach 15 bis 20 Minuten Wartezeit,
Zylinderkopf mit vorgeschriebenem Drehmoment nach Schema, Abb.237,
mit Spezialwerkzeug 21-034 nachziehen. Kipphebelachse nachziehen
und Ventilspiel nochmals überprüfen.
- Zylinderkopfhaube anschrauben,
Zündkabel aufstecken, Abb.238, und Ansauggeräuschdämpfer
montieren.
|
Abb.236 Zündmarkierung
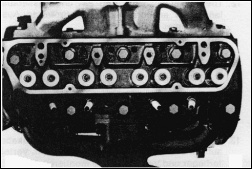
Abb.237 Anzugsreihenfolge Zylinderkopf
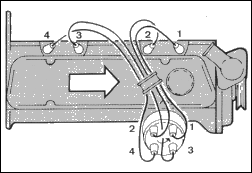
Abb.238 Zündkabelanordnung
(Zündfolge)
|
|
21 165 5
Zylinderkopf auswechseln
(ohne Ventile, Zylinderkopf abgebaut) |
|
ERFORDERLICHE
SPEZIALWERKZEUGE:
Ventilfederspanner |
................................... |
G2-6513-A |
|
|
|
Zerlegen
- Ansaugkrümmer (5 Schrauben)
komplett mit Vergaser und Auspuffkrümmer (6 Muttern) von
Zylinderkopf abbauen, Abb.265.
- Stehbolzen - Auspuffkrümmer (6)
und Temperaturgeber - Fernthermometer herausschrauben.
- Ventilfedern und Teller mit
Spezialwerkzeug G2-6513-A abbauen, Abb.266.
Bei der Demontage und Montage der Ventilfedern ist unbedingt
darauf zu achten, dass der Ventilschaft beim Aus- und Einbau der
Ventilkeile durch den heruntergedrückten Ventilfederteller nicht
beschädigt wird. Bei Beschädigungen des Schaftes ist sonst keine
Gewähr der genügenden Abdichtung gegeben. Es erfolgen
überhöhter Ölverbrauch und Verschleißerscheinungen in den
Ventilführungen.
- Ölabschirmringe abnehmen und
Ventile herausnehmen.
Bei jedem Aus- und Einbau der Ventile sind neue
Ölabschirmringe zu verwenden.
Zusammenbau
Vor dem Zusammenbauen des neuen
Zylinderkopfes sind die eventuell zu übernehmenden Teile des alten
Zylinderkopfes auf Verschleiß und Funktionsfähigkeit zu
überprüfen.
- Ventile und Ventilführungen mit
Öl benetzen. Ventile einsetzen. Ölabschirmringe auf Ventilschaft
schieben, Abb.267.
|
Abb.265 Ansaugkrümmer mit Vergaser
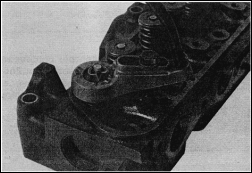
Abb.266 Ventilfedermontage mit
Spezialwerkzeug G2-6513-A
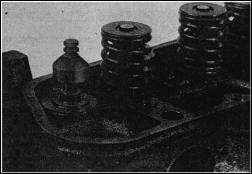
Abb.267 Ölabschirmring auf Ventilschaft
|
- Ventilfedern und Ventilteller mit
Spezialwerkzeug G2-6513-A montieren. Auf richtigen Sitz der
Ventilkeile achten.
- Stehbolzen für Ansaugkrümmer und
Auspuffkrümmer eindrehen. Geber - Fernthermometer einschrauben,
Abb.268.
- Ansaugkrümmer komplett mit
Vergaser, Abb.269, und Auspuffkrümmer mit neuen Dichtungen
anschrauben.
Bei Übernahme eingelaufener Ventile in den neuen Zylinderkopf
ist vor deren Einbau der Ventilteller auf einer
Ventilschleifmaschine unbedingt nachzuschleifen und wie folgt
weiter zu verfahren:
- Ventile in dem Zylinderkopf
einschleifen, Abb.270. Ventile und Ventilsitze von
Schleifpasteresten reinigen, einölen und einsetzen. Weiteren
Reparaturablauf, wie ab Punkt 5 (Ölabschirmringe) beschrieben,
ausführen.
|
Abb.268 Geber - Fernthermometer
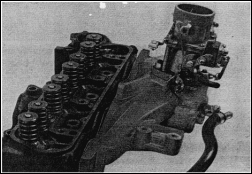
Abb.269 Ansaugkrümmer mit Vergaser

Abb.270 Ventile einschleifen
|
|
21 213
Ventilspiel einstellen |
|
KEIN
SPEZIALWERKZEUG ERFORDERLICH
|
|
- Ansauggeräuschdämpfer entfernen.
Zündkabel von Zündkerzen abziehen und Zylinderkopfhaube abbauen.
- Den Motor während der
Ventilspieleinstellung nur in Motordrehrichtung drehen. Bei der
ersten Ventileinstellung die Kurbelwellen - Riemenscheibe mit der
Markierung auf die "0°-Marke" des Stirnraddeckels
stellen, Abb.292.
Zur Erleichterung bei Beginn der Ventilspieleinstellung auf der
Riemenscheibe einen Kreidestrich anbringen, der eine Unterteilung
von 180° aufzeigt. Dann nach folgendem Schema
Ventilspieleinstellung vornehmen. Einstellwerte siehe Technische
Daten.
Wird die Riemenscheibe jetzt etwas hin- und hergedreht, so
überschneiden sich die Ventile am 1. oder 4. Zylinder, Abb.293,
d. h., beide Kipphebel bzw. Stößelstangen bewegen sich
gegenläufig. Überschneiden sich die Ventile des 4. Zylinders, so
ist das Ventilspiel des 1. Zylinders einzustellen. Wird die
Riemenscheibe um 180° weitergedreht, so überschneiden sich die
Ventile des 3. Zylinders und das Ventilspiel kann am 2. Zylinder
eingestellt werde.
4. Zyl. überschneidet - 1. Zyl. einstellen
3. Zyl. überschneidet - 2. Zyl. einstellen
1. Zyl. überschneidet - 4. Zyl. einstellen
2. Zyl. überschneidet - 3. Zyl. einstellen
- Zylinderkopfhaube aufsetzen und
anziehen. Zündkabel aufstecken, Abb.294, und
Ansauggeräuschdämpfer montieren.
|
Abb.292 Riemenscheibe auf OT-Markierung
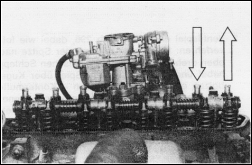
Abb.293 Überschneidung Ventile 4. Zylinder
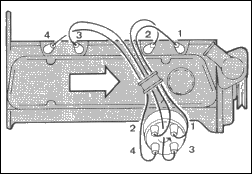
Abb.294 Zündkabelanordnung (Zündfolge)
|
|
21 233 9
Ventilführung aufreiben |
|
ERFORDERLICHE
SPEZIALWERKZEUGE:
Siehe Position Spezialwerkzeuge.
|
|
- Altes Ventil in Ventilführung
stecken und Spiel durch seitliches Drücken ermitteln, Abb.301.
Die Ventilführungen zeigen nach längerer Laufzeit ovalen
Verschleiß. Deshalb beim Nachreiben grundsätzlich von der Ventilsitzseite
her aufreiben. Die zu wählende Bohrungsgröße hängt vom
Verschleiß der Führungsbohrung und der zur Verfügung stehenden
Ventil-Übergröße ab. Beim Reiben, Abb.302, muss immer mit der kleinsten
Reibahle begonnen werden, da für die größeren Reibahlen die
Schnitttiefe zu groß ist.
- Ventilsitz nach vorgeschriebenen
Angaben, siehe Technische Daten,
mit Spezialwerkzeug nachfräsen.
Bevor der Ventilsitz bearbeitet wird, ist es unbedingt wichtig,
dass die Ventilführung kontrolliert oder aufgerieben wird.
|
Abb.301 Ventilführungsspiel durch
seitliches Drücken ermitteln,
"C"-Motor
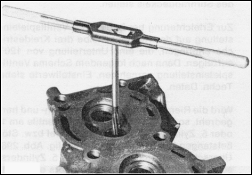
Abb.302 Ventilführung aufreiben,
"C"-Motor
|
|
21 238
Ölabschirmringe -
Ventilschaft auswechseln |
|
ERFORDERLICHE
SPEZIALWERKZEUGE:
Ventilfederspanner |
................ |
G2-6513-A("A")/21-024("C") |
Ventilfederzusatzstück |
...... |
21-024-02("A")/P-6118-3A("C") |
Ventilhalter |
.................................................... |
G2-6513-B |
|
|
|
Ausbauen
- Batterie - Massekabel abklemmen
und Ansauggeräuschdämpfer abnehmen. Lichtmaschine -
"C"-Motor mit Halter komplett abmontieren, Abb.303.
|
Abb.303 Lichtmaschine mit Halter,
"C"-Motor
|
- Keilriemen abnehmen, Zündkabel
von Zündkerzen abziehen und Zylinderkopfhaube(n) abschrauben.
- Zündkerzen ausschrauben und
Kipphebelachse (4 Schrauben) abmontieren. Am "C"-Motor
Kipphebelachsen (6 Schrauben) mit Ölfangblechen abbauen, Abb.304,
und Stößelstangen entfernen.
Stößelstangen und Kipphebelachse(n) beim Aus- und Einbau
nicht vertauschen.
- Ventilhalter G2-6513-B, Abb.305,
in Zündkerzenbohrung einschrauben, gegen Ventilteller stellen und
kontern. Ventilfederspanner G2-6513-A, Abb.305, oder 21-024 mit
Zusatzstücken 21-024-02 und P-6118-3A an Zylinderkopf montieren.
- Die Ventilfeder herunterdrücken,
Ventilfederkeile, Abb.306, entnehmen und Ventilfeder entspannen.
Ventilfederteller, Ventilfeder und Ölabschirmring entfernen.
Bei der Demontage und Montage der Ventilfedern ist unbedingt
darauf zu achten, dass der Ventilschaft beim Aus- und Einbau der
Ventilkeile durch den heruntergedrückten Ventilfederteller nicht
beschädigt wird. Bei Beschädigungen des Schaftes ist sonst keine
Gewähr der genügenden Abdichtung gegeben. Es erfolgen
überhöhter Ölverbrauch und Verschleißerscheinungen in den
Ventilführungen.
|
Abb.304 Kipphebelachse mit Ölfangblech
abbauen, "C"-Motor
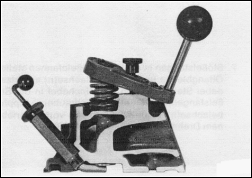
Abb.305 Abbau der Ventilfeder mit
Spezialwerkzeugen am
"C"-Motor
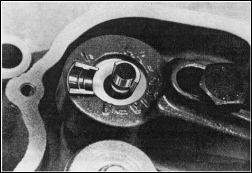
Abb.306 Ventilkeile ausbauen,
"C"-Motor
|
Einbauen
- Neuen Ölabschirmring auf
Ventilschaft stecken, Abb.307. Ventilfeder in umgekehrter
Reihenfolge, wie unter Punkt 5 beschrieben, einbauen.
Spezialwerkzeug entfernen.
- Stößelstangen in die
Ventilstößelpfannen stellen. Ölfangbleche und Kipphebelachse(n)
aufsetzen, dabei Stellschrauben der Kipphebel in die
Stößelstangenpfannen führen. Schrauben - Kipphebelachse(n)
beidrehen und mit vorgeschriebenem Drehmoment anziehen, Abb.308.
- Ventilspiel einstellen, siehe Position
21 213, Zündkerzen einschrauben und Zylinderkopfhaube(n)
anbauen.
- Zündkabel aufstecken,
Ansauggeräuschdämpfer montieren und Batterie - Massekabel
anschließen. Am "C"-Motor Lichtmaschine mit Halter
anschrauben, Abb.309. Keilriemen auflegen und mit Lichtmaschine
spannen.
|
Abb.307 Ölabschirmring auf
Ventilschaft
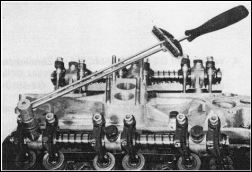
Abb.308 Kipphebelachse mit vorge-
schriebenem Drehmoment
festdrehen, "C"-Motor
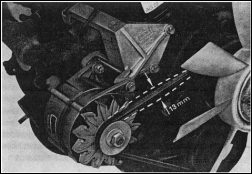
Abb.309 Lichtmaschine mit Halter,
"C"-Motor
|
|
21 467
Radialdichtring - Kurbelwelle
vorn auswechseln |
|
ERFORDERLICHE
SPEZIALWERKZEUGE:
Auszieher,
Kurbelwellendichtring |
..................... |
15-048 |
Zusatzstück |
.............................................. |
15-048-01 |
Einbauring,
Kurbelwellendichtring |
.................... |
21-046 |
|
|
|
Ausbauen
- Batterie- Massekabel abklemmen und
Schutzpappe - Ölwanne abmontieren (4 Schrauben, 4 Clipse).
Kühlflüssigkeit ablassen, dabei Kühlerschläuche von
Wasserpumpe und oben vom Wasserauslassstutzen - Motor entfernen.
- Kühler ausbauen (4 Schrauben).
Lichtmaschine lösen und abkippen. Keilriemen abnehmen. Lüfter (4
Schrauben) und Kurbelwellen- Riemenscheibe (1 Schraube) abbauen,
Abb.342.
- Radialdichtring mit
Spezialwerkzeug 15-048 und Zusatzstück 15-048-01, wie in Abb.343
dargestellt, ausbauen.
Einbauen
- Neuen Radialdichtring (Dichtlippe
leicht eingeölt oder eingefettet) mit Spezialwerkzeug 21-046 in
Verbindung mit der Riemenscheibe und Schraube, wie in Abb.344
dargestellt, einziehen.
- Spezialwerkzeug entfernen, Lüfter
und Riemenscheibe mit vorgeschriebenem Drehmoment montieren.
Keilriemen auflegen und mit Lichtmaschine spannen. Lichtmaschine
befestigen.
- Kühler einbauen.
Kühlerschläuche anschließen und Kühlmittel einfüllen.
- Schutzpappe - Ölwanne montieren
und Batterie- Massekabel anklemmen. Motoröl kontrollieren, ggf.
nachfüllen.
|
Abb.342 Kurbelwellen-Riemenscheibe
mit handelsüblichem
Werkzeug abziehen
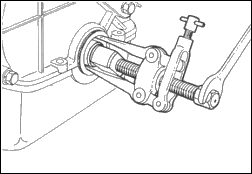
Abb.343 Radialdichtring mit Spezial-
werkzeug ausbauen
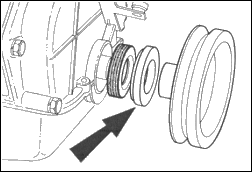
Abb.344 Radialdichtring montieren
|
|
21 505 5
Kolben vom Pleuel ab- und
anbauen |
|
KEIN
SPEZIALWERKZEUG ERFORDERLICH
|
|
Allgemeines
Kolben und Kolbenbolzen bilden eine
Einheit und dürfen nur zusammen ausgetauscht werden. Kolbenbolzenauge
und Kolbenbolzen- Durchmesser sind durch Farbzeichen in Klassen
aufgeteilt und müssen zueinander passen. Der Farbpunkt befindet sich
auf dem Kolbenboden und auf der Außenkante des Bolzens.
Muss eine Zylinderbohrung um 1,0 mm aufgebohrt werden, ist es
erforderlich, die übrigen Zylinderbohrungen um das gleiche Maß
aufzubohren. Eine Ungleichheit der Bohrungen würde zu Störungen
führen, da bei 1,0 mm Übergröße eine Gewichtstoleranz bis zu 10
Gramm möglich ist.
Abbauen
- Sicherungsringe, Abb.359, aus
Kolbenbolzenauge entfernen.
- Kolbenbolzen mit einem geeigneten
Dorn aus dem Kolben heraustreiben, Abb.360.
Anbauen
- Auf einer Seite des Kolbens im
Bolzenauge einen Sicherungsring montieren, Abb.361.
|
Abb.359 Sicherungsring entfernen
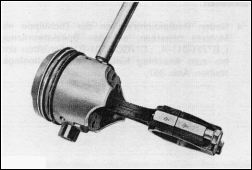
Abb.360 Kolbenbolzen ausbauen
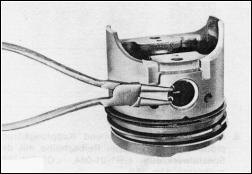
Abb.361 Sicherungsring montieren
|
- Kolben auf einer Heizplatte
erwärmen, Abb.362.
- Pleuelauge mit Öl benetzen und so
in den erwärmten Kolben einschieben, dass das Pleuelauge mit
Kolbenbolzenauge in einer Flucht steht.
- Den Kolbenbolzen durchschieben bis
zum vorher montierten 1. Sicherungsring, Abb.363. Zweiten
Sicherungsring montieren.
Bei der Montage muss die Frontmarkierung des Kolbens (Pfeil,
Kerbe, usw.) mit der Frontmarkierung der Pleuelstange in eine
Richtung zeigen, Abb.364.
|
Abb.362 Kolben erwärmen
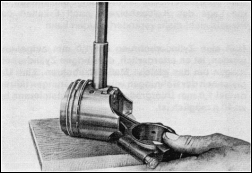
Abb.363 Kolbenbolzen montieren
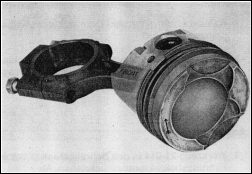
Abb.364 Anordnung der Front-
markierungen zueinander
|
TECHNISCHE DATEN
- Motor "A"
Motor |
1,3
HC |
Motorkennzeichnung
Lage der Nockenwelle
Ventilsteuerung
Zündfolge
Bohrung
Hub
Hubraum
Verdichtungsverhältnis
Kompressionsdruck bei Anlasserdrehzahl
Mittlerer Arbeitsdruck
Leerlauf
Max. Dauerdrehzahl
Motorleistung (DIN)
Drehmoment (DIN)
|
J2E
im Kurbelgehäuse rechts
über Stößelstangen und Kipphebel
1 - 2 - 4 - 3
80,98 mm
62,99 mm
1263 cm3
9,2 : 1
10 ... 12 kp/cm2
9,0 kp/cm2
800 ± 20 1/min
5800 1/min
55 PS bei 5500 1/min
9,3 kpm bei 3000 1/min
|
Zylinderblock |
Gusszeichen im Zylinderblock
Zahl der Hauptlager
Zylinder-Laufbüchsenbohrung
Zylinderbohrung Ø
Standard
A
Zylinderbohrung Ø
Standard
B
Zylinderbohrung Ø
Standard
C
Zylinderbohrung Ø
Standard
D
Zylinderbohrung Ø
Standard
E
Zylinderbohrung Ø
Standard
F
Spurlagerbreite
Montierte Hauptlagerschalen, senkrechter Innen-Ø
Untermaß 0,254
Untermaß 0,508
Untermaß 0,762
Hauptlager
Grundbohrung
Standard
Übergröße
Bohrung für Nockenwellenlagerbüchse Standard
Übergröße
|
711 M-6015-A-A
5
84,112 ... 84,175 mm
80,947 ... 80,957 mm
80,957 ... 80,967 mm
80,967 ... 80,977 mm
80,977 ... 80,987 mm
80,987 ... 80,997 mm
80,997 ... 81,007 mm
26,822 ... 26,873 mm
54,013 ... 54,044 mm
53,759 ... 53,790 mm
53,505 ... 53,536 mm
53,215 ... 53,282 mm
57,683 ... 57,696 mm
58,064 ... 58,077 mm
42,888 ... 42,913 mm
+ 0,508 mm
|
Kurbelwelle |
Hauptlagerzapfen
Ø
Standard
Untermaß 0,254
Untermaß 0,508
Untermaß 0,762
Axialspiel
Länge Hauptlagerschale
Spiel Lagerschale-Hauptlagerzapfen
Pleuellagerzapfen
Ø
Standard
Untermaß 0,05
Untermaß 0,25
Untermaß 0,51
Untermaß 0,76
Untermaß 1,02
|
53,983 ... 54,003 mm
53,729 ... 53,749 mm
53,475 ... 53,495 mm
53,221 ... 53,241 mm
0,075 ... 0,280 mm
25,273 ... 25,527 mm
0,010 ... 0,061 mm
49,195 ... 49,215 mm
49,144 ... 49,164 mm
48,941 ... 48,961 mm
48,687 ... 48,707 mm
48,433 ... 48,453 mm
48,179 ... 48,199
|
Nockenwelle |
Kennzeichnung
Antrieb
Dicke der Nockenwellen-Halteplatte
Hubhöhe der
Nocken
Einlass
Auslass
Länge der
Nocken
Einlass
(zwischen Ferse und
Spitze)
Auslass
Lager-Ø der Nockenwelle, vorn, Mitte, hinten
Innen-Ø der Lagerbüchse, vorn, Mitte, hinten
Axialspiel der Nockenwelle
|
711 F-6250 CC
über Kette und Kettenspanner
4,457 ... 4,508 mm
5,985 mm
5,894 mm
33,087 mm
33, 326 mm
39,616 ... 39,637 mm
39,662 ... 39,675 mm
0,06 ... 0,2 mm
|
Kolben |
Kolben-Ø KD
Standard
Klasse E
Klasse F
Kolben-Ø Übergröße
Klasse E
Klasse F
Kolbeneinbauspiel
Ringstoß
(eingebaut)
oben
Mitte
unten
|
80,954 ... 80,964 mm
80,964 ... 80,974 mm
0,064 mm
81,018 ... 81,028 mm
81,028 ... 81,038 mm
0,023 ... 0,043 mm
0,23 ... 0,36 mm
0,23 ... 0,36 mm
0,23 ... 0,36 mm
|
Kolbenbolzen |
Kolbenbolzenlänge
Bolzen-Ø 1
2
3
4
Überdeckung im Kolben bei 21° C
Spiel im Pleuel bei 21° C
|
70,99 ... 71,37 mm
20,622 ... 20,625 mm
20,625 ... 20,627 mm
20,627 ... 20,630 mm
20,630 ... 20,632 mm
0,003 ... 0,008 mm
0,004 ... 0,010 mm
|
Pleuelstange |
Bohrungs-Ø großes Auge
Bohrungs-Ø kleines Auge weiß
rot
gelb
blau
Senkrechter Innen-Ø
Standard
Untermaß 0,051
Untermaß 0,254
Untermaß 0,508
Untermaß 0,762
Untermaß 1,016
Spiel Pleuelzapfen - Lagerschale
|
52,89 ... 52,91 mm
20,629 ... 20,632 mm
20,632 ... 20,634 mm
20,634 ... 20,637 mm
20,637 ... 20,640 mm
49,221 ... 49,260 mm
49,170 ... 49,208 mm
48,967 ... 49,005 mm
48,713 ... 48,751 mm
48,491 ... 48,592 mm
48,205 ... 48,243 mm
0,006 ... 0,064 mm
|
Zylinderkopf |
Gusszeichen am Zylinderkopf
Ventilsitzwinkel im Kopf
Schaftbohrung, Einlass- und Auslassventil
Bohrung für Buchsen |
A
44° 33' ... 45°
7,907 ... 7,937 mm
11,133 ... 11,153 mm
x
Abb.385 Ventilsitzwinkel
A = Ventilsitz - Einlass
B = Ventilsitz - Auslass
|
Ventile |
Ventilspiel, Einlass
Auslass
Einlassventil öffnet
schließt
Auslassventil öffnet
schließt
Ventilfeder - Anzahl der Windungen
Ventilstößel Ø
Stößelspiel im Gehäuse
|
0,20 mm
0,56 mm
21° v OT
55° n UT
70° v UT
22° n OT
3,75 oder 5,75
13,081 ... 13,094 mm
0,013 ... 0,05 mm
|
Einlassventil |
Länge
Ventilteller Ø
Ventilschaft
Ø
Standard
Übergröße 0,074
Übergröße 0,381
Spiel Ventilschaft in der Führung
Ventilhub
|
Total 111,2 mm
38,02 ... 38,28 mm
7,868 ... 7,886 mm
7,945 ... 7,962 mm
8,249 ... 8,267 mm
0,02 ... 0,068 mm
8,379 mm
|
Auslassventil |
Länge
Ventilteller Ø
Ventilschaft
Ø
Standard
Übergröße 0,074
Übergröße 0,381
Spiel Ventilschaft in der Führung
Ventilhub
|
Total 110,65 mm
31,34 ... 31,59 mm
7,846 ... 7,863 mm
7,922 ... 7,939 mm
8,227 ... 8,243 mm
0,043 ... 0,091 mm
8,251 mm
|
Motorschmierung |
Ölsorte
Viskosität
Ford-Spezifikation
Erstfüllmenge mit Filter
Ölwechsel ohne Filterwechsel
Ölwechsel mit Filterwechsel
Mindest-Öldruck bei 700 1/min
bei 2000 1/min
Öldruck-Kontroll-Licht leuchtet auf bei
Überdruckventil öffnet bei
Ölpumpe Spiel äußerer Rotor - Gehäuse
Spaltmaß Innen/Außenrotor
Axialspiel äußerer und innerer Rotor
zum Ölpumpendeckel
|
HD-Öl
unter -12° C: SAE 5W/20
unter 0° C: SAE 5W/30
-23° C bis +32° C: SAE 10W/30
oder: SAE 10W/40
oder: SAE 10W/50
über -12° C: SAE 20W/40
oder: SAE 20W/50
SS-M2C-9001AA
3,67 Liter
2,75 Liter
3,25 Liter
0,6 kp/cm2
1,5 kp/cm2
0,4 ± 0,1 kp/cm2
2,46 ... 2,81 kp/cm2
0,1397 ... 0,2667 mm
0,0508 ... 0,1270 mm
0,0254 ... 0,0635 mm
|
Anzugsdrehmomente |
Hauptlagerdeckel
Pleuelschrauben
Kurbelwellenriemenscheibe
Nockenwellenkettenrad
Dichtringträger hinten
Schwungrad
Stirnraddeckel
Ölpumpe
Ansaugleitung
Ölpumpendeckel
Kipphebelachse
Zylinderkopf
1)
2)
3)
nach 10 bis 20 Minuten Wartezeit 4)
nach dem Warmlaufen des Motors
(15 Min bei 100 1/min) nachziehen 5)
Zylinderkopfhaube
Ölwanne
1)
2)
Ölablassschraube
Öldruckschalter
Zündkerzen
Ansaugkrümmer
Auspuffkrümmer
Kraftstoffpumpe
Kupplungsdruckplatte an Schwungrad
Wasserpumpe
Wasserstutzen - Thermostatgehäuse
Lüfter an Wasserpumpenflansch
|
75 ... 82 Nm (7,5 ... 8,2 kpm)
42 ... 48 Nm (4,2 ... 4,8 kpm)
33 ... 38 Nm (3,3 ... 3,8 kpm)
17 ... 21 Nm (1,7 ... 2,1 kpm)
17 ... 21 Nm (1,7 ... 2,1 kpm)
68 ... 76 Nm (6,8 ... 7,6 kpm)
07 ... 10 Nm (0,7 ... 1,0 kpm)
17 ... 21 Nm (1,7 ... 2,1 kpm)
17 ... 21 Nm (1,7 ... 2,1 kpm)
07 ... 10 Nm (0,7 ... 1,0 kpm)
24 ... 30 Nm (2,4 ... 3,0 kpm)
00 ... 07 Nm (0,0
... 0,7 kpm)
28 ... 42 Nm (2,8 ... 4,2 kpm)
70 ... 76 Nm (7,0 ... 7,6 kpm)
90 ... 97 Nm (9,0 ... 9,7 kpm)
90 ... 97 Nm (9,0 ... 9,7 kpm)
3,5 ... 05 Nm (0,35 ... 0,5 kpm)
04 ... 07 Nm
(0,4 ... 0,7 kpm)
08 ... 11 Nm (0,8 ... 1,1 kpm)
27 ... 34 Nm (2,7 ... 3,4 kpm)
13 ... 15 Nm (1,3 ... 1,5 kpm)
30 ... 39 Nm (3,0 ... 3,9 kpm)
17 ... 21 Nm (1,7 ... 2,1 kpm)
21 ... 25 Nm (2,1 ... 2,5 kpm)
16,3 ... 20,3 Nm (1,63 ... 2,03 kpm)
17 ... 21 Nm (1,7 ... 2,1 kpm)
07 ... 10 Nm (0,7 ... 1,0 kpm)
17 ... 21 Nm (1,7 ... 2,1 kpm)
07 ... 10 Nm (0,7 ... 1,0 kpm) |
|